1、引言
化工行業是國民經濟的重要組成部分,其生產過程涉及多種復雜的化學反應和物理變化,因此對設備的要求極為嚴格。機械設計制造技術憑借其高精度、高效率和高可靠性的特點,成為化工設備制造中的關鍵技術。本文旨在探討機械設計制造技術在化工設備中的具體應用,以滿足化工行業生產過程中對設備的高標準要求。
2、機械設計制造技術的概念
機械設計制造技術是指運用科學原理和工程方法,將各種機械系統和零部件從構思、設計、開發、制造到最終成形的全過程。它涉及材料科學、力學、熱學、動力學、控制理論和計算機技術等多個學科,是現代工業生產的核心技術。機械設計是機械制造技術的前提和基礎。它包括從需求分析、概念設計、詳細設計到優化設計的全過程[1]。在這個過程中,設計工程師需要考慮機械系統的功能、性能、成本、可靠性、可制造性和可維護性等多個因素。現代機械設計還廣泛應用計算機輔助設計(CAD)技術,通過三維建模和仿真技術,提高設計效率和準確性。同時,機械制造是將設計轉化為實際產品的關鍵環節。它包括材料選擇、加工工藝、裝配工藝和質量控制等多個方面。現代機械制造技術的發展,使高精度、高效率和高柔性的制造成為可能。數控機床、工業機器人、增材制造(3D打印)等先進制造技術的應用,極大地提升了機械制造的水平和能力。此外,機械設計制造技術還包括對制造過程的監控和優化。利用傳感器、數據采集和分析技術,可以實時監控制造過程中的各種參數,及時發現和解決問題,提高產品質量和生產效率。智能制造和工業4.0的概念正在推動機械制造向更加智能化、數字化和網絡化的方向發展。
3、機械設計制造技術在化工設備中的應用內容
機械設計制造技術在化工設備中的應用主要包括結構設計與優化、設備布置、設備安裝、設備維護等。其中,結構設計是化工設備設計的基礎,合理的結構設計不僅可以提高設備的生產效率,還能延長設備的使用壽命。在結構設計中,材料選擇、應力分析、熱力學分析等都是至關重要的環節。通過應用先進的計算機輔助設計(CAD)軟件,設計人員可以對設備的結構進行精確建模和模擬,從而發現并解決潛在問題,提高設計的科學性和合理性。設備布置涉及化工設備在生產線上的合理安排。科學的設備布置不僅可以提高生產效率,還能降低能耗和運營成本。在設備布置過程中,需要綜合考慮設備的功能、操作便捷性、安全性和維護方便性。同時,合理的設備布置還能有效減少設備之間的干擾,提高整個生產系統的穩定性和可靠性[2]。設備安裝是將設計轉化為現實的關鍵步驟。高效的設備安裝需要嚴格按照設計圖紙和工藝要求進行,同時需要保證安裝過程中的安全性和精度。先進的安裝技術,例如,激光對準技術和自動化安裝系統的應用,可以顯著提高安裝的精度和效率,減少安裝過程中的人為誤差。設備維護是保證設備長期穩定運行的重要環節。通過引入預測性維護技術,利用傳感器和數據分析技術,可以實時監測設備的運行狀態,提前發現和解決潛在問題,避免設備的非計劃停機和故障。定期維護保養不僅可以延長設備的使用壽命,還能提高設備的運行效率和安全性。同時利用維護管理系統(CMMS)。
4、機械設計制造技術在化工設備中的應用
4.1設備選型
以某大型化工企業為例,該企業在新建一條生產線時,采用了先進的機械設計制造技術對反應釜、蒸餾塔、換熱器等關鍵設備進行了科學選型。通過動態模擬,該企業優化了工藝流程,提高了設備的利用率;通過性能參數匹配和材料選擇,確保了設備的高效運行和長壽命;通過經濟性分析,降低了生產成本;同時,嚴格的環保和安全性評估,使生產過程更加綠色和安全。因此,對于反應釜的選型,企業選擇了具有高效攪拌功能和良好耐腐蝕性能的不銹鋼反應釜。根據不同的反應條件,還配置了夾套和內盤管,以保證熱交換效率和反應溫度的均勻性[3]。而蒸餾塔選擇了一種具備高分離效率和低能耗的填料塔。根據生產需求,蒸餾塔內填充了不同材質和規格的填料,以實現最佳的分離效果。塔體采用耐高溫、耐腐蝕的材料制造,確保了長時間運行的穩定性和可靠性。此外,蒸餾塔配備了先進的自動控制系統,可以實時監測和調整操作參數,保證了蒸餾過程的精確性和穩定性。對于換熱器的選型,企業根據熱交換需求和介質特性,選擇了高效的板式換熱器。該換熱器具有傳熱系數高、熱損失小、結構緊湊和維護方便等優點。
通過優化換熱器的流道設計,提高了熱傳導效率,減少了能源消耗。同時,換熱器的材質選用了耐腐蝕性能優異的不銹鋼,延長了設備的使用壽命。
4.2設備布置
在設備選型確定之后,合理的設備布置設計是確保化工生產線高效、安全運行的關鍵。該大型化工企業在布置設計過程中,充分利用了機械設計制造技術,進行了科學、系統的規劃和布局。因此,通過計算機輔助設計(CAD)軟件,建立了整個生產線的三維模型。在這個模型中,反應釜、蒸餾塔和換熱器等設備的具體位置、管道走向以及其他附屬設施一目了然。這不僅有助于優化空間利用,還可以提前發現并解決潛在的干涉問題,確保每臺設備都能在最佳位置運行,最大限度地提高生產效率。同時,采用了有限元分析(FEA)技術,對關鍵設備和支撐結構進行了應力分析和強度校核。通過模擬各種工況下設備的受力情況,確保了設備和管道系統在運行過程中不會出現因應力集中而導致的結構性損壞,從而提升了整個系統的可靠性和安全性。在工藝管道設計方面,企業結合流體力學原理和CFD(計算流體動力學)仿真技術,優化了管道的布置和規格。通過仿真分析,確定最佳的管道直徑和流速,減少了流動阻力和能量損失,確保了介質的平穩輸送。同時,合理設置了管道的支撐和補償裝置,避免了因溫度變化導致的熱脹冷縮對管道系統的影響。此外,企業還注重設備的維護和檢修便利性。在布置設計中,充分考慮了設備的操作空間和檢修通道,確保操作人員能夠方便地進行日常維護和故障排除。通過設立合理的檢修平臺和通道,減少了停機時間,提高了設備的可維護性和運行效率。
4.3設備安裝
在設備安裝前,通過三維激光掃描技術對安裝現場進行了精確測量和建模。利用這些數據,企業能夠準確了解現場的空間布局和實際條件,確保設備安裝的精度和協調性。這一過程有效避免了安裝過程中可能出現的誤差和偏差,確保了設備與管道、支撐結構的精準對接。在安裝過程中,采用了先進的自動化安裝設備和工具。例如,使用機器人進行焊接和組裝,不僅提高了安裝的精度和效率,還減少了人工操作的誤差和勞動強度。同時,企業借助智能吊裝設備,對大型設備進行精準定位和安裝。通過自動化控制系統,吊裝設備能夠實時調整設備的位置和角度,確保安裝過程的順利進行。
為了保證設備安裝質量,企業在安裝過程中進行了嚴格的質量檢測和控制。利用無損檢測技術,如超聲波檢測、射線檢測和磁粉檢測,對焊接接頭和關鍵部位進行了全面檢查,及時發現并處理潛在的質量問題。此外,企業還采用了在線監測系統,對設備安裝的全過程進行實時監控和記錄,確保每一個安裝步驟都符合設計要求和標準。在設備安裝完成后,企業進行了系統的調試和測試工作。通過對每臺設備的單機調試和聯動調試,確保設備的運行參數和工藝要求相匹配。例如,在反應釜的調試過程中,通過對攪拌速度、加熱溫度和反應壓力的調試,確保了反應過程的穩定性和高效性。在蒸餾塔的調試過程中,通過對填料的分布和操作參數的調整,確保了分離效果和能耗的最優化。化工設備安排流程如圖1所示。
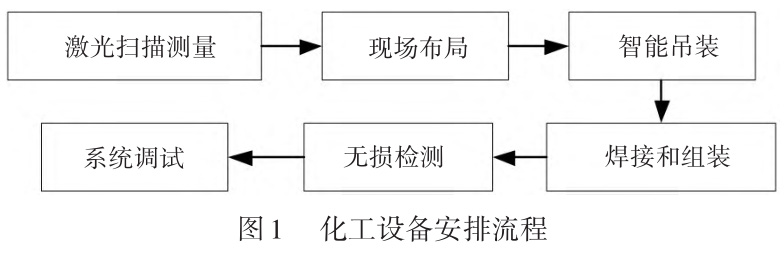
4.4設備維護
為了防止設備的非計劃停機和突發故障,采用了定期維護與預防性維護相結合的方法。通過建立詳細的設備維護計劃,定期對設備進行檢查、清潔和保養,確保設備始終處于最佳工作狀態。利用基于物聯網(IoT)的智能監測系統,實時采集設備運行數據,如振動、溫度、壓力等關鍵參數。借助大數據分析技術,可以提前發現設備的潛在問題,并根據預測結果安排預防性維護,避免設備故障對生產造成的影響。同時,通過遠程監控與診斷系統,技術人員可以隨時隨地監控設備的運行狀態,并進行遠程診斷和故障排除。例如,在反應釜的監控中,系統可以實時顯示攪拌速度、溫度和壓力等參數,當出現異常時,系統會自動報警并生成故障報告。技術人員通過遠程訪問系統,分析故障原因并制定相應的維
修方案,從而減少現場維護的時間和成本。此外,為了提高維護管理的效率,企業引入了先進的維護管理系統(CMMS)(見圖2),通過該系統,企業可以全面管理設備的維護記錄、維修歷史和備件庫存,實現維護工作的數字化和智能化。維護管理系統還集成了數據分析功能,可以對設備的運行數據進行深入分析,找出影響設備性能的關鍵因素,并提出改進措施。例如,通過分析反應釜的運行數據,可以發現影響攪拌效果的因素,并對攪拌系統進行優化設計。
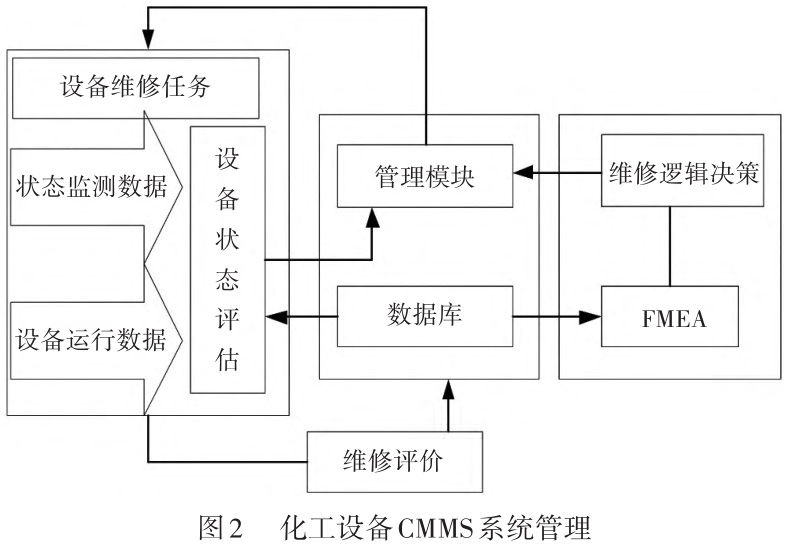
5、結束語
綜上所述,機械設計制造技術在化工設備中的應用,不僅為化工企業提供了高效、可靠的生產設備,還在設備選型、布置設計、安裝及維護等各個環節中發揮了重要作用。通過科學選型,企業能夠根據實際需求選擇最合適的設備,從而提高生產效率和產品質量;通過合理布置,最大化空間利用,確保設備的穩定運行;通過精確安裝,減少可能的誤差和偏差,確保設備的最佳初始狀態;通過智能維護,預防設備故障,延長設備使用壽命,確保生產過程的連續性和穩定性。
參考文獻
[1]張福星.智能制造技術在機械加工領域中的應用[J].現代制造技術與裝備,2023,59(05):150~152
[2]趙波慧.機械設計制造技術在化工設備中的應用[J].化學工程與裝備,2023,(08):208~209+223
[3]鄭則興.機械制造技術在化工設備中的應用[J].造紙裝備及材料,2020,49(03):17
作者簡介:王祎聰,男,1988年8月生,漢族,山東東營人,本科,研究方向:機械設計制造及自動化。
相關鏈接