鈦分離器、鈦蒸發器、鈦反應釜是三種以鈦或鈦合金為主要材料制造的工業設備,因其優異的耐腐蝕性和特定功能,廣泛應用于化工、制藥、海洋等領域。這三種常見的鈦設備,所具有性能、制作工藝、應用、選購方法等,騰宇鈦業結合多年的鈦設備深加工及銷售,結合相關資料,淺析如下:
一、各設備特點對比
1、鈦分離器
定義:鈦分離器是利用物理或化學方法將混合物(氣液、液液或固液)中的不同組分進行分離的設備。其核心結構采用鈦或鈦合金制造,以抵抗強腐蝕性介質(如鹽酸、氯離子、高溫酸性溶液等)的侵蝕。
性能:耐強酸(如鹽酸、硫酸)、耐氯離子腐蝕;分離效率高,適用于氣液或液液分離。
材質:工業純鈦(TA1/TA2)或鈦合金(TA9/TA10)。
執行標準:GB/T 14845(板式換熱器相關)、ASME BPE(衛生級標準)。
制作工藝:焊接采用TIG/等離子焊,內壁拋光至Ra≤0.4μm(制藥級)。
應用領域:化工精餾、制藥萃取、海水淡化預處理。

2、鈦蒸發器
定義:鈦蒸發器是一種通過加熱使溶液中的揮發性溶劑蒸發,從而實現溶液濃縮或溶質分離的熱交換設備。鈦材質使其適用于高腐蝕性、高溫介質的蒸發過程。
性能:傳熱系數高(鈦導熱性優于不銹鋼),抗結垢性強,適用于高溫濃縮。
材質:TA2(常規)、TA10(含鉬鎳,耐高溫酸性介質)。
執行標準:GB/T 25151.3-2010(蒸發器專項標準)。
制作工藝:管板脹接+密封焊,多效設計提升能效。
應用領域:鹽化工母液濃縮、核廢水處理、鋰電池材料蒸發。
3、鈦反應釜
定義:鈦反應釜是一種用于進行化學反應、合成或混合過程的密閉容器,主體由鈦或鈦合金制成,可耐受強酸、強堿及高溫高壓環境,并配備攪拌、加熱/冷卻等輔助系統。
性能:耐壓≤6.4MPa,耐溫-20~300℃,帶變頻攪拌(轉速可調)。
材質:TA2主體+TA9內襯(局部增強防腐)。
執行標準:GB/T 25151.1-2010(高壓反應釜國標)。
制作工藝:整體鍛造封頭,內壁鏡面拋光(電化學拋光)。
應用領域:醫藥中間體合成、氯化法鈦白粉生產、高端染料反應。
二、選購指南
1、關鍵參數匹配
介質特性:含Cl?>500ppm必須選鈦;含HF需改用哈氏合金。
溫度/壓力:超300℃需鈦鈀合金(TA9);高壓工況選鍛件結構。
認證要求:ASME認證(出口設備)、GMP認證(制藥行業)。
2、工藝優化建議
蒸發器宜選升膜式(高沸點溶液)或降膜式(熱敏物料)。
反應釜攪拌器選錨式(高粘度)或渦輪式(高效混合)。
3、供應商評估
查看壓力容器A1/A2資質,鈦材需提供TA2/TA10材質證書。
案例考察:同類行業成功應用(如氯堿行業蒸發器案例)。
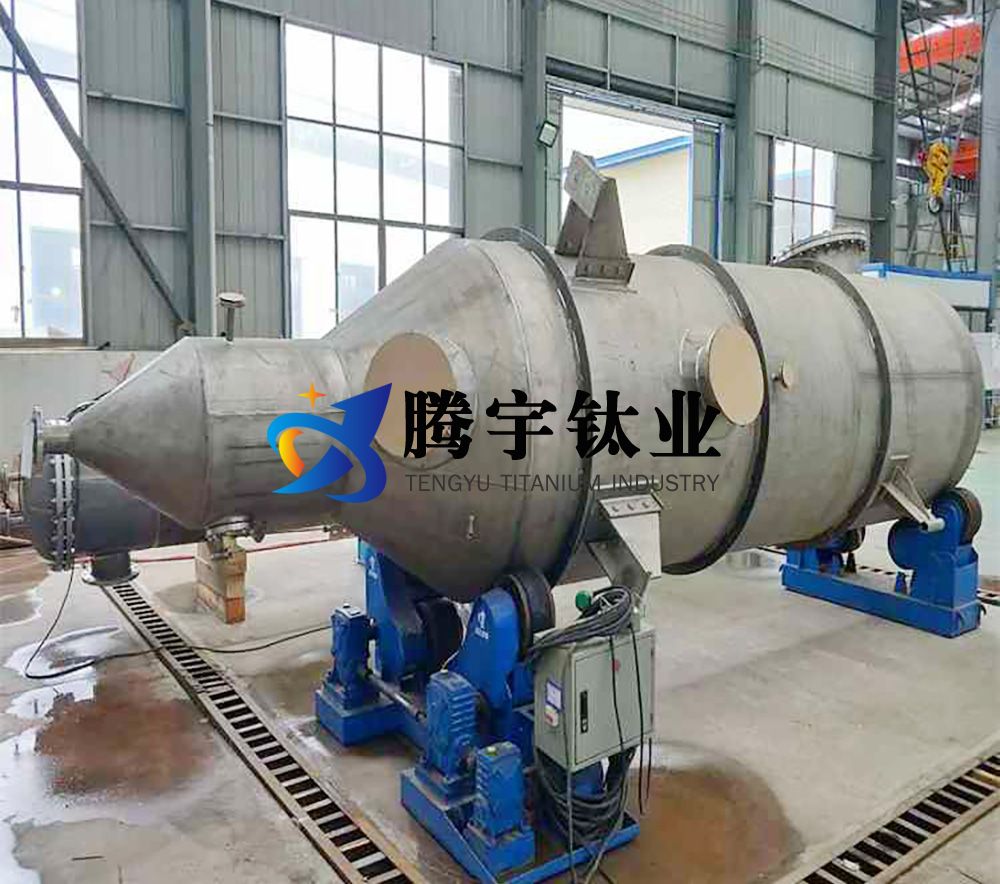
三、使用注意事項
1、防交叉污染
禁止與碳鋼工具直接接觸(鐵離子污染引發點蝕)。
專用吊裝工具(尼龍吊帶),避免機械損傷。
2、操作規范
升溫速率≤50℃/h(防熱應力裂紋)。
停機時需用去離子水沖洗(防結晶物殘留)。
3、維護要點
每年PT檢測焊縫,重點檢查氣液交界處腐蝕。
密封件更換周期:氟橡膠2年,PTFE 5年(視工況調整)。
四、成本優化策略
復合結構設計:非接觸部位采用鈦鋼復合板(降低成本30%)。
模塊化選型:小批量生產選標準型號(交貨期縮短50%)。
再生利用:舊設備可通過酸洗(HF+HNO3混合液)恢復性能。
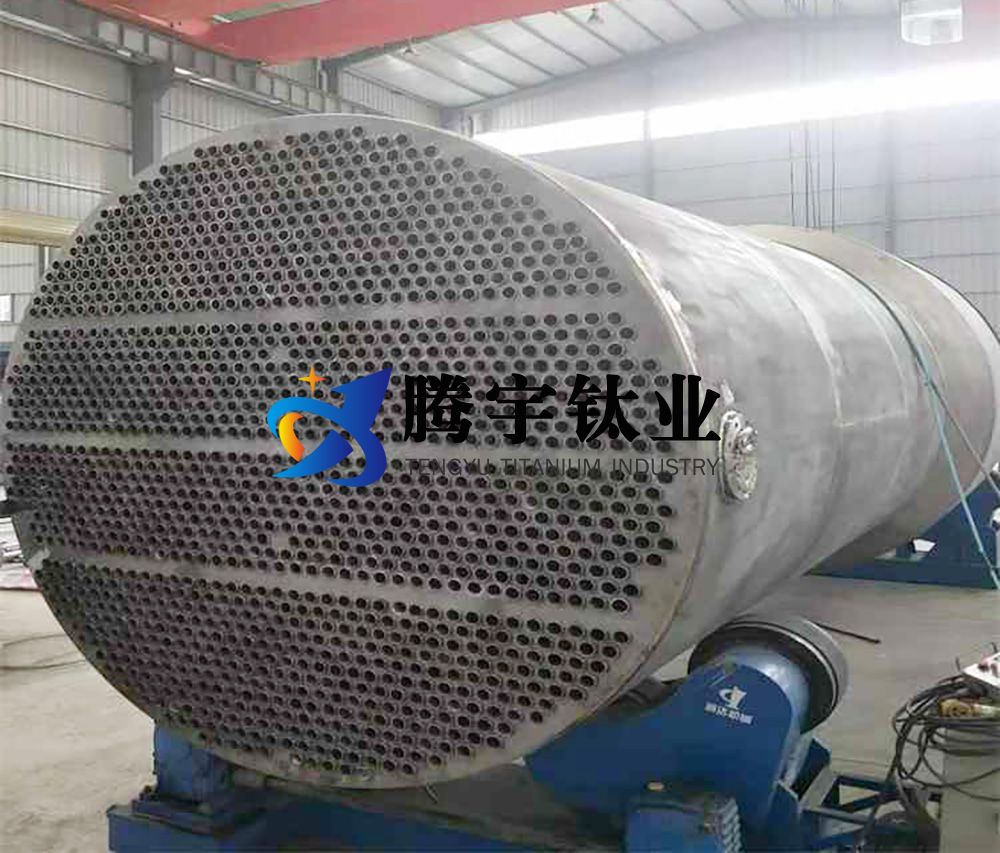
通過精準匹配工況需求與設備特性,可最大限度發揮鈦設備的耐腐蝕優勢,延長使用壽命至20年以上。建議與具備冶金背景的供應商深度合作,實現全生命周期成本最優。
相關鏈接