引言
TC4合金作為一種典型的 α-β 型兩相鈦合金,密度小、比強度高、耐蝕耐熱性能好,被廣泛應用于航空、航天、軍工等領域[1]。 隨著越來越多的鈦產品涌入民用領域,TC4鈦合金開始被廣泛研究。 國內多位學者通過高溫下TC4鈦合金的熱壓變形,研究了變形溫度及變形速率對材料流變應力的影響,并結合微觀組織演變確定了材料最佳變形溫度及變形速率范圍[2-4]。 寶鈦集團、西部鈦業等鈦產品生產制造企業[5-6] 采用不同的軋制工藝及熱處理工藝對TC4鈦合金板坯進行軋制實驗,通過對試樣進行金相分析和力學性能測試,探究了最優軋制工藝。 王牛俊等人[7] 對TC4鈦合金進行鍛造熱塑性變形加工,然后進行多火次換向熱軋變形,研究了其組織演變規律。 徐勇等人[8]通過多道次軋制制備了高強度TC4鈦合金板材,比較分析了多道次換向軋制和單向軋制的TC4鈦合金室溫力學性能和微觀組織。 目前研究多圍繞在TC4鈦合金熱變形特性研究及軋制工藝開發方面,對于熱軋過程板坯溫度變化及其全流程溫度控制方面研究鮮有報道。
鈦合金軋制與常規鋼材軋制不同,其軋制溫度窗口窄,導熱性能差,若開軋溫度過高或軋制變形過大均會導致軋件心部溫度急劇升高,組織出現缺陷、塑性變差,導致軋制變形不均、板帶邊裂等問題;軋制溫度過低,將導致軋制力過大,板形難以控制等問題。 此外,軋制溫度也直接影響軋制力模型的準確性進而影響軋件出口厚度精度。
鈦合金板材熱軋生產目前仍依賴人工經驗,采用“邊看邊軋”方式,其自動化程度相比先進鋼鐵生產具有很大差距[9]。 因此,系統研究多道次熱軋過程鈦合金板材溫度變化及分布規律,變形及力能參數變化等對于實現鈦合金板材生產自動化、提升產品良品率及生產效率至關重要。
本文采用 MSC. Marc 有限元軟件進行TC4鈦合金板多道次熱軋全流程模擬,重點研究多道次軋制過程中軋件表面與心部溫度變化情況,分析軋件表面與心部溫差變化原因,為制定TC4鈦合金板合理熱軋工藝規程,實現鈦合金軋制生產自動化提供理論依據。
1 、多道次軋制過程有限元模型
將鈦合金板材熱軋過程視為對稱問題,取二分之一進行分析,建立如圖 1 所示平面軋制模型。
由于軋件與軋輥間的接觸換熱主要發生在輥面,將工作輥設為可傳熱剛性空心輥[9],經模擬驗證后設置空心輥厚度為 50mm,以縮短計算時間。軋件咬入依靠軋件后端一速度略低于工作輥線速度的剛性推板強迫推入輥縫,咬入后該剛體自動被釋放,軋件在摩擦力的作用下實現穩定軋制。
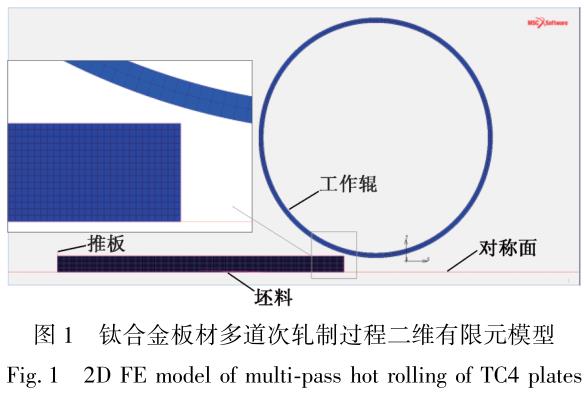
提取上一道次溫度場數據,作為下一道次各節點溫度初始條件輸入,實現鈦合金板材多道次熱軋過程溫度場的繼承。 本文只針對軋件中部溫度場進行研究,故不考慮軋件頭尾溫差,軋件模擬長度進行了縮短處理,根據軋制速度、軋制長度等工藝條件延長各道次間隙空冷時間,補充由于截短軋件而減少的軋制時間。
軋制模擬過程基本參數見表 1。 通過熱軋實驗、空冷實驗結合有限元模擬的方法[10],確定了TC4軋件與軋輥接觸換熱系數為 8000W·m-2·K-1、軋件與空氣對流換熱系數為 120
W·m-2 ·K-1。TC4鈦合金材料熱物參數參照文獻[11] 進行設置,見表 2。 流變應力根據 Gleeble-3800 熱模擬實驗機上測得的材料流變數據編制[12-13]。
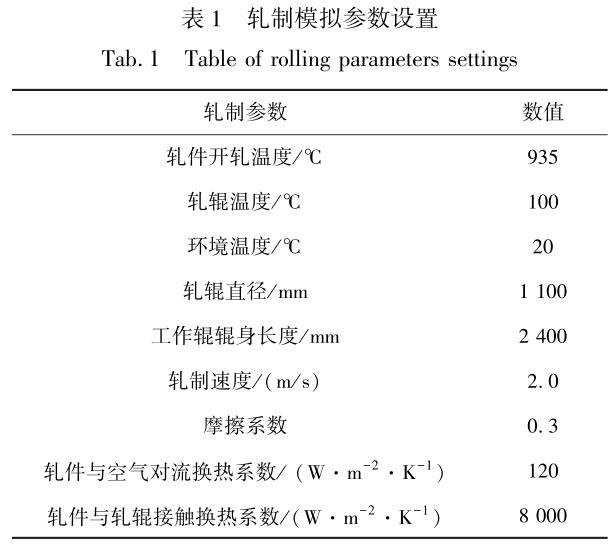
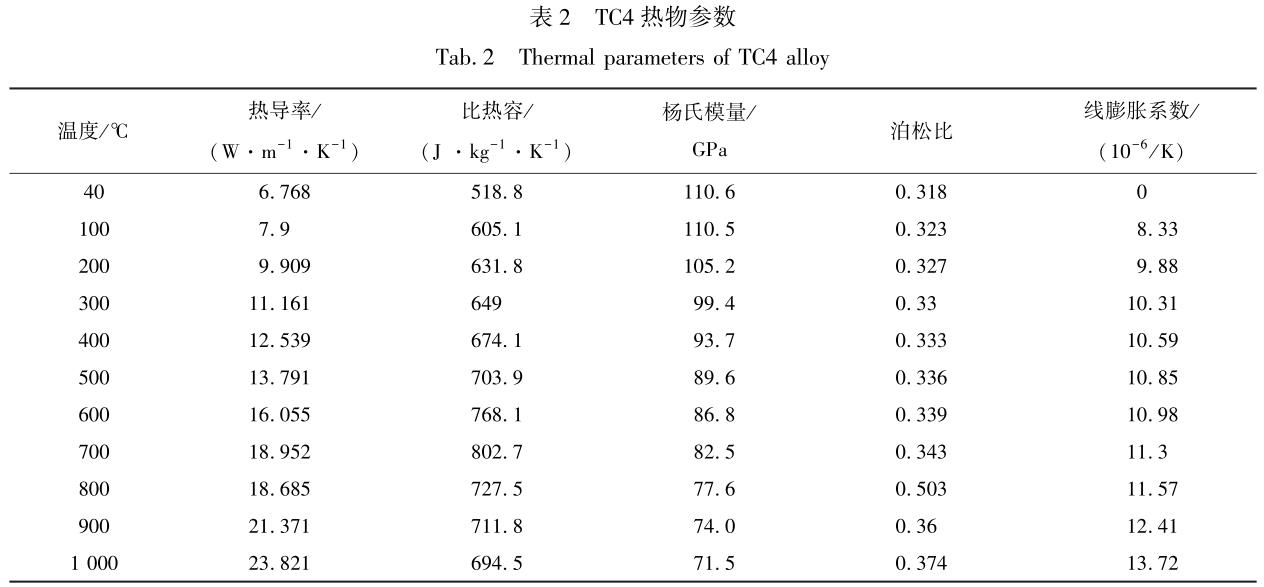
軋制工藝制度采用某廠TC4鈦合金板軋制現場工藝數據,第一火次軋制分為 8 個道次,各道次軋制工藝參數見表 3,原始板坯尺寸為 150mm(厚)×1800mm(長) ×2700mm(寬)。 針對該規程建立有限元模型進行仿真模擬,分析一火次軋制中鈦合金板坯溫度分布及演變規律,并提取各道次軋制力與溫度的模擬結果,并與實際軋制結果進行對比,驗證有限元模型的準確性。
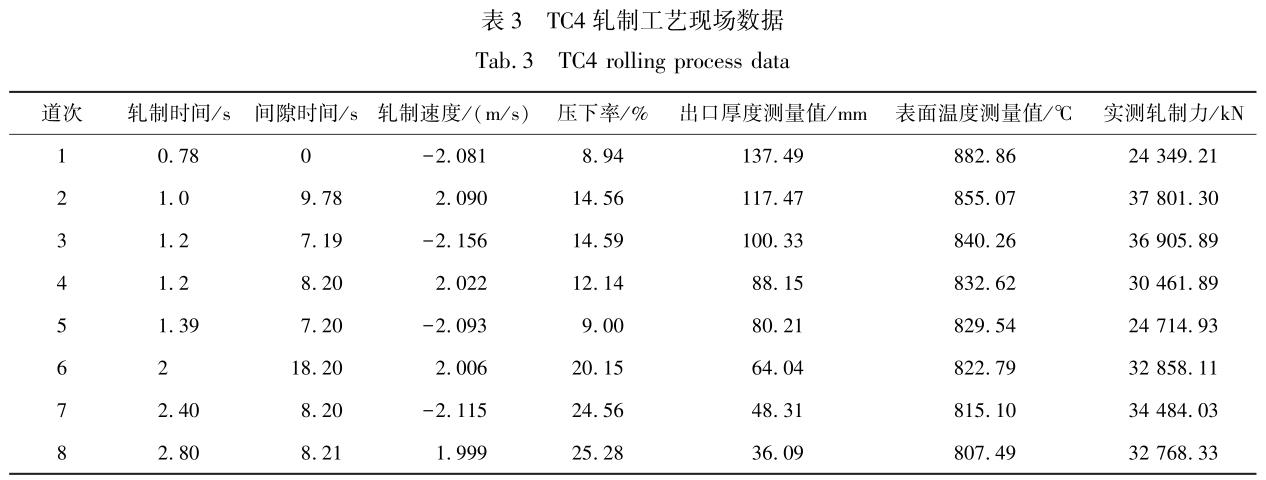
2 、結果及分析
2. 1 溫度結果分析
鈦合金板軋制過程中對溫度控制要求較為嚴格,故本文重點研究軋件心部溫度與表面溫度變化情況。 各道次軋后板坯厚度方向溫度場云圖分布如圖 2。 隨著軋制道次的進行,鈦板坯溫降在厚度方向上逐漸由表面向心部推移,在板坯厚度較大時,表面溫度不斷降低,在第 7,8 道次由于軋件減薄內部熱傳導占據主要作用,表面溫度小幅升高;而心部溫度經 8 道次軋后變化不大。
軋后板坯表面和心部平均溫度變化如圖 3。
隨著軋制的進行,在初始幾個道次軋件較厚時,表面與心部溫差不斷增大,到第 6 道次最大溫差達到 120℃;而第 7 道次后軋件變薄,軋件內部熱傳導占據主導地位,軋件整體溫度開始趨于均勻,軋件表面溫度與心部溫度的溫差減小。
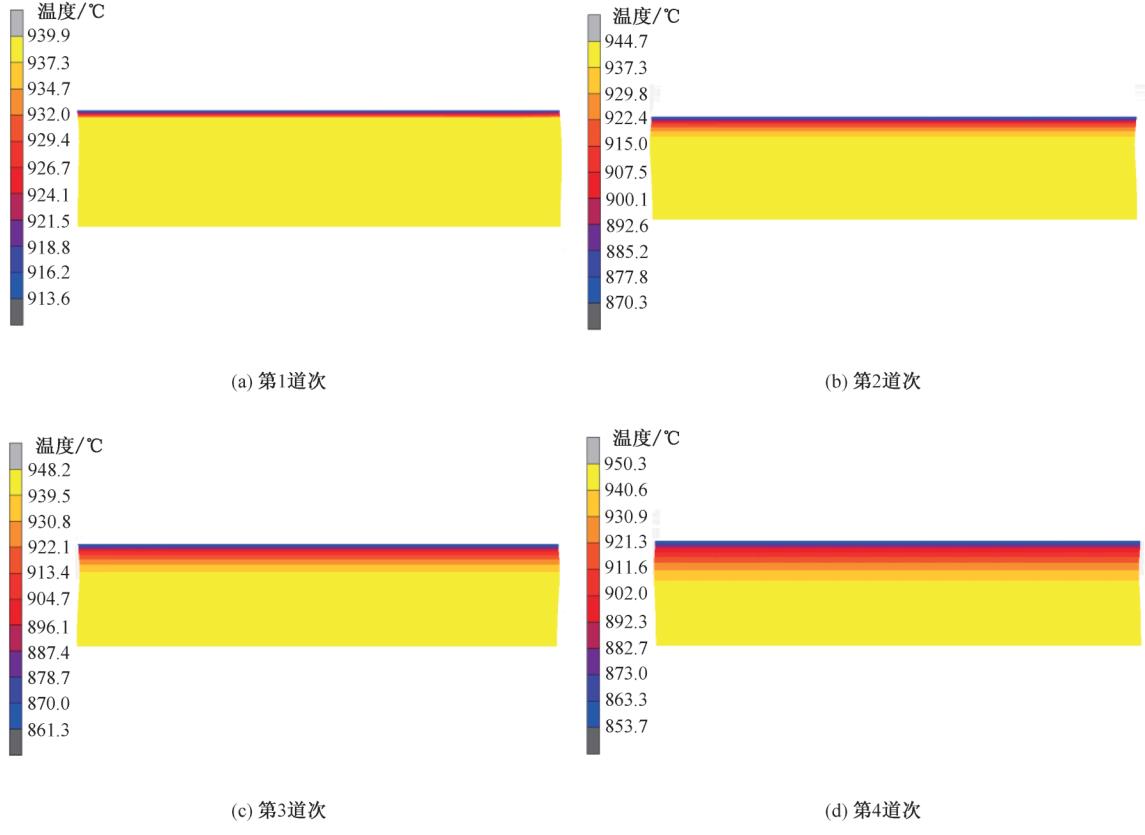
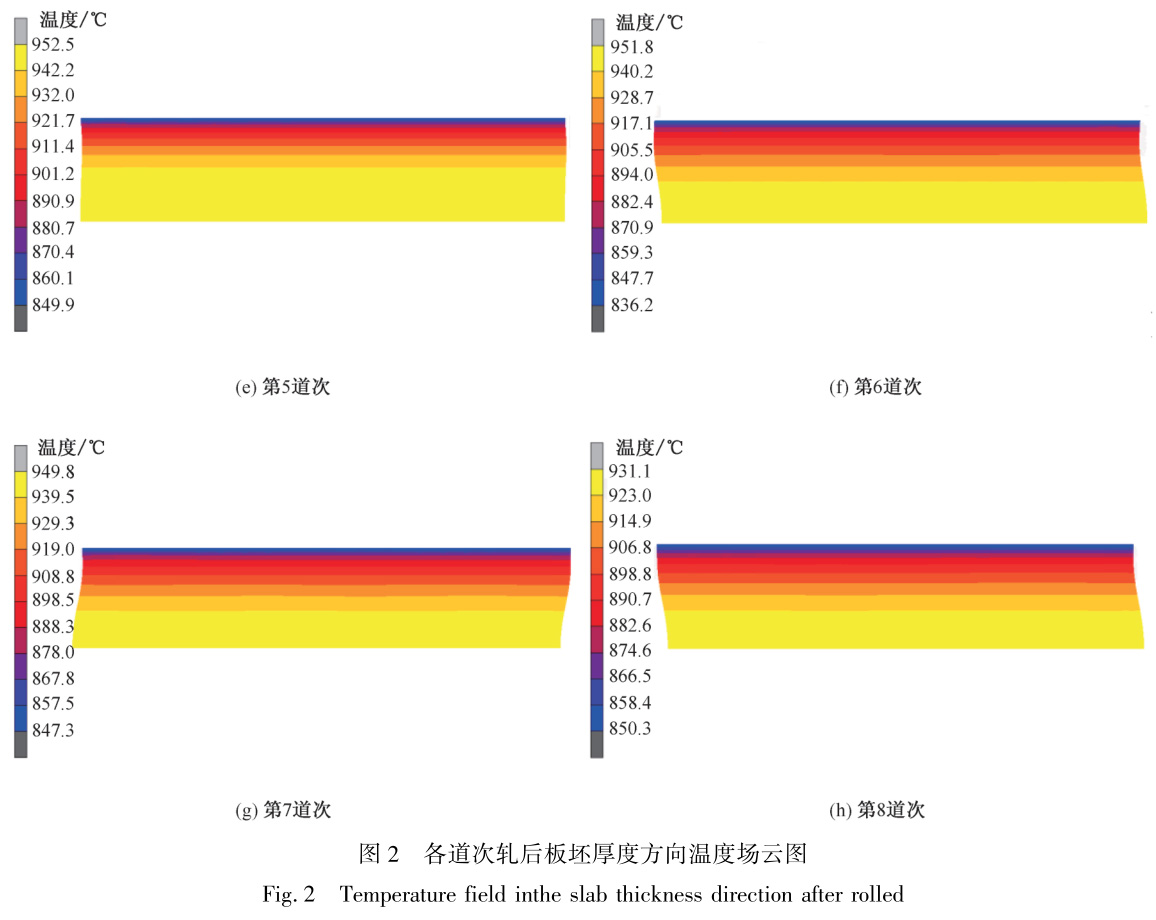
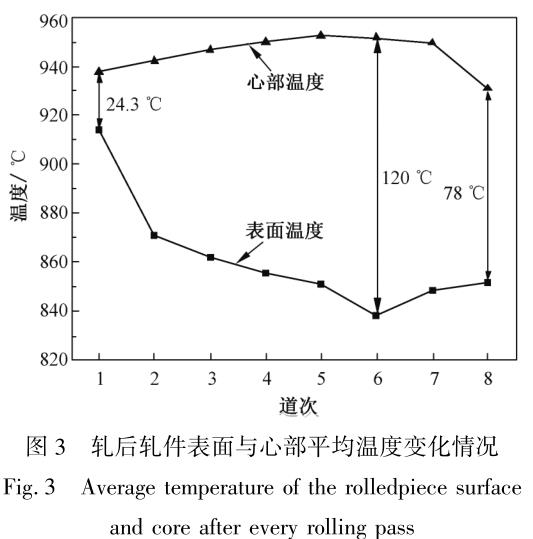
第一火次軋制全流程中軋件表面與心部溫度變化曲線如圖 4 所示。 由于空冷、與軋輥接觸換熱溫降較大,且空冷速度約 1℃ / s,每道次由軋輥接觸換熱引起的溫降約 20℃ 左右,表面溫度在軋制全流程中整體呈不斷降低的趨勢,至第 8 道次出軋制區后軋件表面溫度降至約 850℃;軋件心部溫度呈先增大后減小的變化趨勢,溫升主要是由軋件內部塑性變形熱量累積引起,至第 5 道次心部溫度最高約 953℃,累計溫升約 20℃,不同道次由于道次壓下率不同,由塑性功生熱引起的心部溫升在 2~5℃ 范圍不等,且壓下率越大溫升越大。
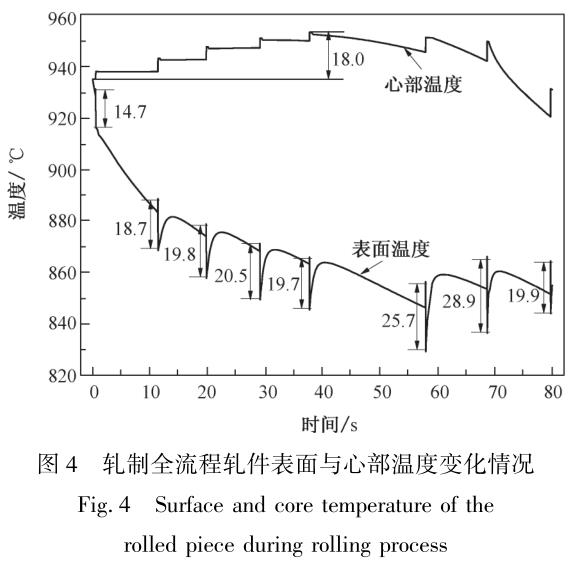
在整個軋制過程中,軋件的溫度變化主要發生在軋制階段,此階段軋件除存在空冷、與軋輥間的接觸換熱等溫降因素外,還有軋件塑性變形生熱、軋件與軋輥摩擦生熱等溫升因素。 故取各道次軋件表面與心部兩位置點從進軋制區到出軋制區的整個軋制階段的溫度變化曲線如圖 5。
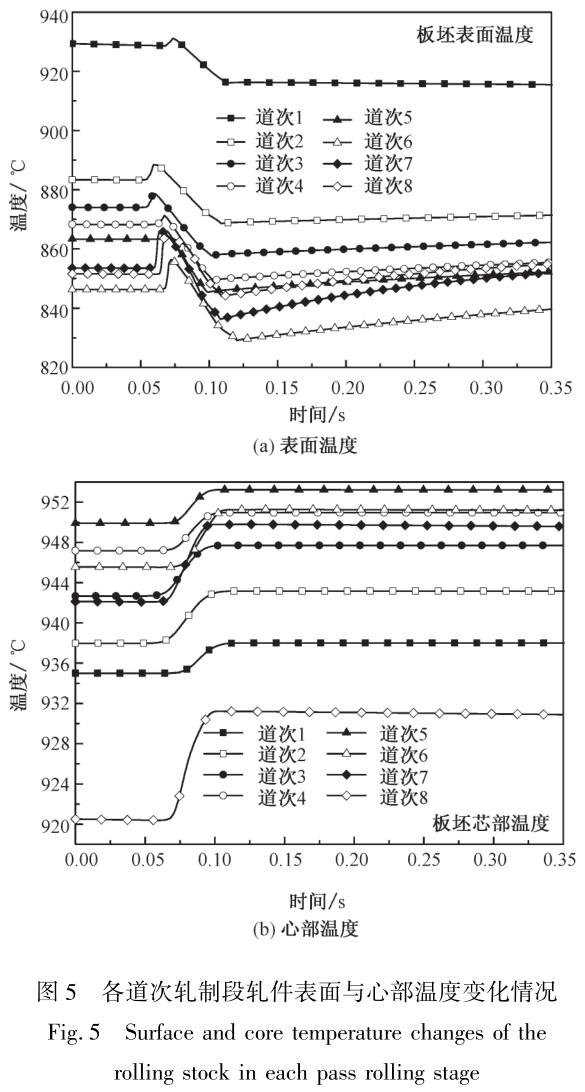
由圖 5 可以看出在各軋制道次中,表面位置點在咬入瞬間,由于軋件和軋輥間的摩擦及塑性功生熱,存在 3~12℃ 的溫升,這主要與各道次軋件與軋輥的接觸狀態有關,之后由于軋輥間接觸,表面溫度急速下降,溫降約為 15~30℃,出軋制區后由于軋件自身熱傳導,又會有不同程度的“ 返紅”現象;而在變形區內軋件心部溫度由于塑性功生熱而出現溫升現象,其溫升情況主要取決于軋制壓下率,第 8 道次軋制壓下率最大為 25. 28%,其溫升達 12℃。 且前 5 道次間心部溫度為不斷累計溫升,到第 6 道次由于軋件減薄,軋件內部開始溫降,且由于軋件
變長、空冷時間增加,軋件整體溫度明顯下降。
2. 2 模擬結果與現場數據對比
提取各道次軋件表面溫度與軋制力的模擬結果,與現場實測結果進行對比,結果如圖 6,圖 7所示。
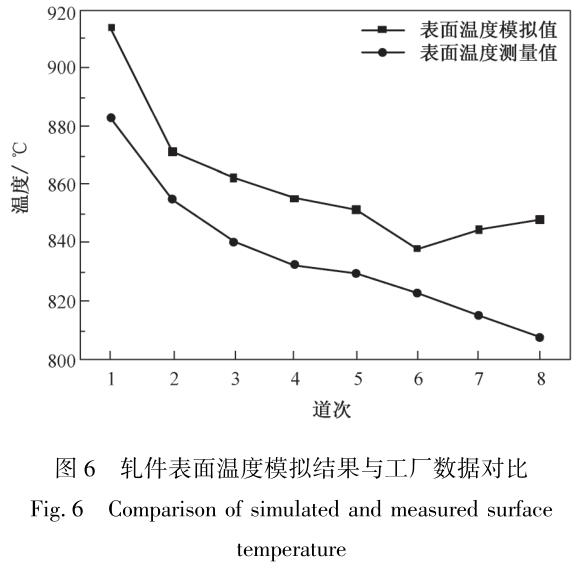
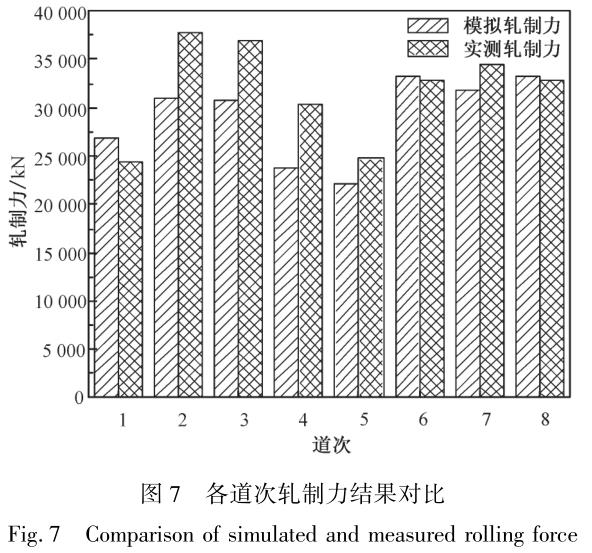
由圖 6 可以看到不同道次下,模擬的表面溫度均高于實測的表面溫度,其原因為模擬開軋溫度與實際開軋溫度存在一定誤差,現場數據無開軋溫度數據。 且由于實際現場中軋件表面溫度采用非接觸式測量,現場測量結果存在一定誤差,總體表面溫度模擬值與實測值吻合性高,誤差限在1. 85% ~ 5. 47%之間。 由軋制力模擬值與實測值對比圖可知,模擬得到的各道次穩定軋制力和實際測量的軋制力有相同的變化趨勢。 最大誤差限在第 2 道次,為 17. 86%,模擬結果在可靠誤差范圍內。
3、 結論
在鈦合金多道次軋制全流程中,隨著軋制道次的進行,軋件表面溫度與心部溫度的溫差呈先增大后較小的變化趨勢,在第 6 道次軋件表面溫度與心部溫度的最大溫差可達120℃。 表面溫差過大易形成較大熱應力從而導致表面開裂。
在各道次軋制時變形區內軋件心部溫度均由于塑性功變形生熱而升高,且心部溫度在前 5 道次不斷溫升,累計溫升約 20℃。 所以在TC4鈦合金熱軋一火次階段,軋件厚度較大時應控制道次壓下率不宜過大,一般不應超過 25%,以防板坯心部溫度越過相變點,塑性變差。
對比模擬得到的軋件表面溫度、各道次穩定軋制力與現場實測表面溫度、軋制力發現模擬結果均在允許誤差范圍內,說明本文建立的TC4鈦合金板材多道次軋制有限元模型可靠,其分析結果對實際制定鈦合金多道次軋制工藝規程具有一定的指導意義。
參考文獻
1、朱知壽 王紅紅 黃旭. 先進航空鈦合金材料與應用 M . 北京國防工業出版社 2012 47-48.
ZHUZS WANGHH HUANGX. Advancedaviationtitaniumalloymaterialsandapplications M . Beijing NationalDefenseIndustryPress 2012 47-48.
2、趙迪.TC4鈦合金壓縮變形行為研究 J . 南方金屬 2015618-20.
ZHAOD. StudyoncompressivedeformationbehaviorofTC4titaniumalloy J . SouthernMetal 20156 18-20.
3、羅皎 李淼泉 李宏 等.TC4鈦合金高溫變形行為及其流動應力模型 J . 中國有色金屬學報 2008 18 8 1395-1401.
LUOJ LIMQ LIH etal. HightemperaturedeformationbehaviorandflowstressmodelofTC4titaniumalloyJ . TheChineseJournalofNonferrousMetals 2008 18 8 1395-1401.
4、白嬌嬌.TC4鈦合金的高溫壓縮變形行為 J . 金屬熱處理2017 42 5 121-126.
BAIJJ. TemperaturecompressiondeformationbehaviorofTC4titaniumalloyJ . MetalHeatTreatment 2017 42 5 121-126.
5、王儉 李有華 李蒙 等. 軋制工藝和退火溫度對 TC4ELI 鈦合金厚板顯微組織的影響 J . 有色金屬材料與工程 2018 393 32-35.
WANGJ LIYH LIM etal. EffectofrollingprocessandannealingtemperatureonmicrostructureofTC4ELItitaniumalloythickplate J . NonferrousMetalMaterialsand
Engineering 201839 3 32-35.
6、歐陽文博 謝英杰 付文杰 等. 軋制工藝對TC4中厚板組織及力學性能的影響 J . 熱加工工藝 2014 43 17 58-60.
OUYANGWB XIEYJ FUWJ etal. EffectofrollingprocessonmicrostructureandmechanicalpropertiesofTC4platesofmiddlethickness J . HotWorkingTechnology 2014 43 17 58-60.
7、王牛俊.TC4鈦合金板熱軋過程顯微組織研究 J . 機械設計與制造工程 2017 46 6 81-83.
WANGNJ. MicrostructurestudyofTC4titaniumalloysheetduringhotrolling J . MechanicalDesignandManufacturingEngineering 2017 46 6 81-83.
8、徐勇 楊湘杰 樂偉 等. 多道次軋制TC4鈦合金微觀組織與力學性能研究 J . 特種鑄造及有色合金 2017 37 7 697-700.
XUY YANGXJ LEW etal. MicrostructureandmechanicalpropertiesofTC4titaniumalloybymultipassrolling J . SpecialCastingandNon-ferrousAlloys 2017 37 7 697-700.
9、周佳. 高溫合金鋼板多道次可逆熱軋的有限元模擬 D . 上海上海交通大學 2009 30-32.
ZHOUJ. Finiteelementsimulationofmulti-passreversinghotrollingforhightemperaturealloy D . Shanghai ShanghaiJiaoTongUniversity 2009 30-32.
10、彭艷. 冶金軋制設備技術數字化智能化發展綜述 J . 燕山大學學報 2020 44 3 218-237.
PENGY. ReviewondevelopmentofdigitalandintelligentmetallurgicalrollingequipmenttechnologyJ .JournalofYanshanUniversity 2020 44 3 218-237.
11、唐廣波 劉正東 康永林 等. 熱軋帶鋼傳熱模擬及變形區換熱系數的確定 J . 鋼鐵 2006 47 5 36-40.
TANGGL LIUZD KANGYL etal. SimulationofthermalevolutionofstripanddeterminationofheattransfercoefficientindeformationzoneduringhotrollingJ . Journal
ofIronandSteel2006 47 5 36-40.
12、陸燕鈴. TA2、TC4熱軋工藝制度研究 D . 上海 上海交通大學 2009 18-20.
LUYL. ResearchonTA2 TC4hotrollingprocesssystem D .Shanghai ShanghaiJiaoTongUniversity 2009 18-20.
13、陳雷 郭曉敏 賈偉 等. 航空用近 β 鈦合金 TC18 熱變形過程中流變應力預測 J . 燕山大學學報 2018 42 6 486-492.
CHENL GUOXM JIAW etal. Predictionofflowstressduringthermaldeformationofnear-βtitaniumalloyTC18foraviationJ . JournalofYanshanUniversity 2018 42 6 486-492.
14、許成.TC4鈦合金板材熱軋工藝研究 D . 秦皇島 燕山大學2018 46-48.
XUC. StudyonhotrollingprocessofTC4titaniumalloysheetD . Qinhuangdao YanshanUniversity 2018 46-48.
相關鏈接