為了實現輕量化目標,進一步提升產品性能,薄壁類零件在航空航天領域得到了日益廣泛的應用。由于薄壁類結構的剛度有限,材料去除量大,隨之而來的是對零件加工精度與加工效率的巨大挑戰。國內外學者主要通過合理分配精加工余量、調節切削參數、刀具參數等,達到控制加工變形,實現薄壁件精密加工的目的。
Liu等針對切削力引起工件彈性變形的誤差補償問題,提出一種基于動態特征的實時變形誤差補償方法,建立動態特征模型,然后根據動態特征模型計算變形量,最終實現了基于功能塊的彈性變形加工誤差補償。潘建建立了以平均加工變形量和加工時間為目標、工藝參數為優化變量、期望最低加工精度可靠度為約束的優化模型,并運用直接補償和迭代補償法對加工誤差進行了補償,得到了滿足預期加工精度的最優工藝參數組合,減小了加工變形量。譚靚等人通過正交試驗發現,在一定范圍內刀具螺旋角增大,會引起軸向力增大,導致切削振動加劇,切削過程不穩定,從而使表面粗糙度增大。鄧亞弟等通過單因素對比試驗法得出隨著刀具螺旋角的增加,刀具與工件的接觸刃長度增加,軸向力Fz 較Fx 、Fy 增大更加明顯。田汝坤通過刀具結構對腹板變形影響極差分析得出結論,刀具螺旋角越大,薄壁腹板變形越大,故加工腹板時應該選用小螺旋角立銑刀。張攀、陳蔚芳提出利用變銑削厚度方法,通過有限元分析,得到恒定切削參數下的讓刀量,再通過切削參數、切削力和讓刀量迭代計算獲得需補償量,從而得到相對欠切量最小的走刀軌跡。
綜合現有研究現狀,國內外學者圍繞薄壁件加工變形問題相繼研究了許多控制方法,但仍有很多問題有待進一步完善。目前的研究多是以框類、梁類等弱剛性零件位為研究對象,研究對象單一、結構形式簡單,研究成果不具有通用性,不適用于本文中鈦合金超薄壁板的加工。
從現有參考文獻可知刀具的螺旋角對薄壁件的加工有重要影響,在一定范圍內,螺旋角越小薄壁件變形越小,但對于螺旋角為0°的直刃型立銑刀研究較少。本文對直刃型銑刀進行展開研究,經過測試發現,螺旋型立銑刀加工時Fz 在正負雙向間往復,對腹板產生“上拉——下壓”的循環作用。而直刃型立銑刀(螺旋角為0°)的Fz 則在正向(垂直工作臺指向地面為正向) 區間內波動,一直下壓鈦合金板材。真空吸盤的吸附效果受到負壓大小、吸盤直徑、密封條布置位置和壁板底面粗糙度、面積等內外部因素影響,具有不確定性。相較之下,在采用真空吸盤的基礎上,使用直刃型立銑刀更有助于腹板的精密加工,可有效避免吸附力不足導致的腹板過切。
考慮徑向切深對側壁變形的影響機制,在較大徑向切深條件下,同樣的加工余量走刀次數減少,工件在切削過程中殘余剛度相對較大;繼續增加徑向切深,雖然工件殘余剛度提高,但是切削力也進一步增大,對刀具的壽命也有較大影響,兩個因素綜合影響時,切削力成為主要影響因素。故而設計合適的精加工余量成為抑制側壁變形的有效方法。
本文根據該鈦合金超薄壁板零件的特點,針對試加工中發生的腹板過切、側壁欠切的問題,對相關原因進行了分析研究,采用不同于常規的螺旋型立銑刀的直刃型銑刀進行加工研究。提出了用直刃型立銑刀加工薄壁腹板,精密設計側壁精加工余量的鈦合金壁板精密高效加工工藝方案。通過實際加工驗證了該方案能夠保證零件加工精度、提升加工效率,有力推動了產品的批產工作。
1、鈦合金超薄壁板的結構
鈦合金超薄壁板的結構如圖1所示,其主體結構為1mm厚的腹板,平面尺寸跨度較大,長760mm,寬 290mm,腹板上帶有多邊形型腔結構,型腔側壁的壁厚為0.5mm,高度為3.5mm,型腔內部的腹板厚度僅為0.5mm,側壁結構的厚度/高度比為1/7,腹板的厚度/ 側壁高度比也為1/7,屬于典型的弱剛度結構。超薄壁板的毛坯為5mm厚鈦合金板材,材料去除率達到了 92.6%。
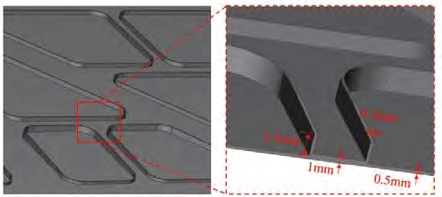
圖1 超薄壁板零件結構示意圖
2、薄壁壁板加工的難點分析
2.1 薄壁腹板過切現象
真空吸盤的吸附效果受到負壓大小、吸盤直徑、密封條布置位置和壁板底面粗糙度、面積等內外部因素影響,具有不確定性。在試驗加工中,鈦合金板材由壓板壓緊邊緣同時使用真空吸盤吸附,使用常規的螺旋型立銑刀加工型腔內腹板,頻繁發生腹板局部過切甚至被過切的問題,嚴重影響了零件的加工精度與成品率。
從真空吸附實況和刀具切削力試驗出發對這一問題進行了分析。零件腹板為薄壁,同時采用螺旋型立銑刀進行切削,此時根據實際測量切削力Fx 、Fy 、Fz 進 行分析,工件受到的Fz 正負交替,當工件的表層受到負向(垂直工作臺指向地面為正向)Fz 的作用,形成向上的牽引效果,同時與真空吸附力發生對抗,當刀具行至轉角處時,切削量增大,Fz 增加至大于真空吸附力時,被加工表面加工中被去除的材料厚度4.5mm,而腹板僅有0.5mm的厚度由于腹板厚度尺寸較小,剛度弱,極易發生過切撕裂。如圖2所示。
2.2 側壁加工欠切問題
壁板內型面的型腔側壁厚度0.5mm,高度3.5mm, 厚度/高度比達到了1/7,屬于典型的薄壁結構,在試加工中發現側壁厚度超差,即所謂的欠切問題。由于側壁的剛度弱,在加工中受到切削力的作用發生彈性變形,薄壁頂部的彈性變形大于根部的彈性變形,因此加工后的薄壁結構往往頂部壁厚偏大,而根部壁厚則能滿足精度要求,如圖3所示。
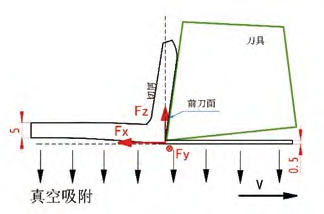
圖2 腹板過切機理
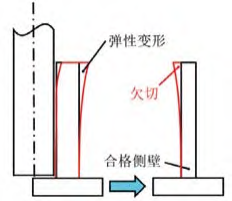
圖3 薄壁加工的彈性變形
3、試驗
3.1 試驗方案
3.1.1 直刃型立銑刀加工腹板
根據上述分析,提出采用直刃型立銑刀控制軸向切削力方向的方法以避免腹板的過切。與常用的螺旋型立銑刀不同,直刃型立銑刀的螺旋角為0°。為了驗證所設計的直刃型立銑刀的切削力方向,使用螺旋型立銑刀與新設計的直刃型立銑刀(見圖4)對TA15 鈦合金板材進行切削試驗,在相同切削參數下測量并對比兩種刀具的切削力。試驗用的兩種銑刀均由刀具提供,刀具的硬質合金材質、涂層等均相同,銑刀的結構參數列于表1。
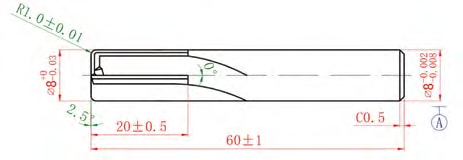
圖4 D8R1直刃型立銑刀的結構
表1 切削力對比試驗使用的兩種刀具
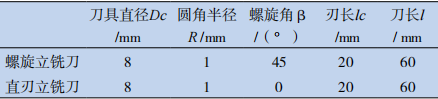
切削試驗在三坐標加工中心上進行,切削參數見表2。使用壓電測力儀及其配套的測量系統測量切削力。Fx 為進給方向切削力,Fy 為切寬方向切削力。軸向切削力Fz 以垂直工作臺指向地面為正向,即被加工材料受到向下的壓力,負向則相反。
表2 切削力對比試驗的切削參數

3.1.2 設計側壁加工余量
針對薄壁加工的彈性變形問題,工藝方案從利用零件自身結構剛度的角度出發,通過預留足夠余量的方法提高薄壁結構的加工精度。為薄壁的精加工預留足夠的余量后,在加工過程中可以利用未加工部分的剛度作為對薄壁的輔助支撐,以此抑制側壁彈性變形導致的欠切問題。
試驗設置4種精加工余量(0.5,1,1.5, 2mm)進行分析。在側壁精加工中,預留的余量將被一次性切除到位,因而試驗中切寬的尺寸即是精加工余量的尺寸。仿真中對應各加工余量而加載的切削力由切削試驗直接測得,試驗使用D8R1直刃型立銑刀切削TA15鈦合金板材。試驗的各項切削參數見表3。
表3 不同精加工余量的切削力試驗參數
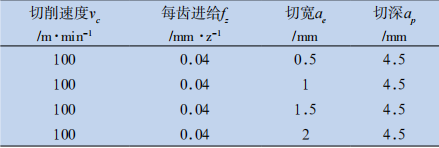
3.2 試驗結果
3.2.1 直刃型立銑刀與螺旋型立銑刀切削力對比
對比試驗結果:螺旋型立銑刀與直刃型立銑刀兩者的切削力的變化分別如圖5(a) 與(b)所示。螺旋型立銑刀的Fz在正負雙向間往復,而直刃型立銑刀的Fz 則在正向區間內波動。由此可以驗證對壁板腹板過切原因的推測。當使用螺旋型立銑刀面銑腹板時,由于腹板厚度僅為0.5mm,Fz 上下往復對腹板產生“上拉——下壓”的循環作用,一旦板材局部厚度不均勻存在翹曲凸起,刀刃切入后將發生過切的問題。而使用直刃型立銑刀切削時Fz 則一直下壓鈦合金板材,因此可以避免腹板過切。此外,還可以發現在試驗參數下直刃型立銑刀的切削力相對螺旋型立銑刀的更小,能夠降低切削過程中產生的殘余應力。因此,直刃型立銑刀適合薄腹板加工。
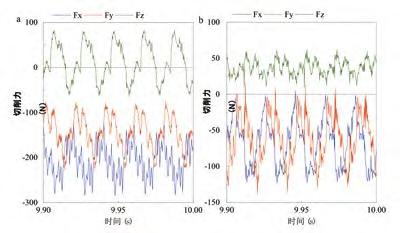
(a) 螺旋銑刀的切削力 (b) 直刃銑刀的切削力
圖5 兩種刀具切削力變化
3.2.2 不同側壁精加工余量設計試驗結果 設
置4種精加工余量(0.5,1,1.5, 2mm)進行試驗測得的切削力如圖6所示,其中Fy 為切寬方向(垂直于側壁)的切削力。在相同條件下,預留更多的精加工余量使得Fy 逐步增加,同時預留更多余量時,前序切削產生的殘余應力更小,更有利于精加工時切削。
將測得的切削力輸入有限元分析算例,對不同余量下的側壁結構在切削力作用下的變形進行分析。有限元分析軟件是Abaqus,楊氏模量為1.18e5MPa,密度 為4.45e-9t/mm3 ,泊松比為0.39。4組余量的側壁的最大法向變形仿真結果如圖7所示,較大余量對應的側壁法向最大變形量相對更小。相比試加工中應用的0.5mm余量,設置較大的余量能夠增強加工中的側壁剛度,對抑制側壁的壁厚超差有顯著的幫助。根據切削力試驗的結果,考慮到直徑D8的刀具切削載荷不宜過大, 因此側壁的精加工余量(即精加工的切寬)也不應一 味增大。參考仿真結果,當精加工余量大于等于1mm 時,最大變形少于0.05mm,即加工的百分比誤差小于 10%,處于精度范圍內,因此設置側壁精加工余量為 1.5mm,實現側壁的精密加工。
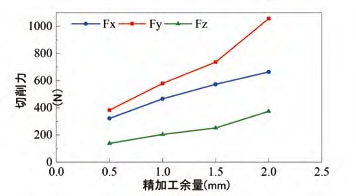
圖6 4種切寬的切削力
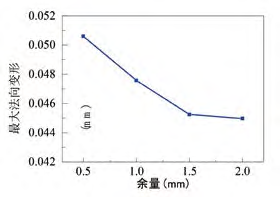
圖7 不同余量側壁最大法向變 形仿真結果
4、試驗結果應用
將上述試驗結果應用至鈦合金超薄壁板腹板和側壁加工中,在解決了技術問題的基礎上,試加工過程穩定,因此增大腹板切削參數,切寬不變,進給速度從原本100mm/min提升至175mm/min,提升加工效率75%。加工出成品零件如圖8,對零件的側壁厚度尺寸進行檢測,其側壁厚度理論尺寸0.5mm,設計要求尺寸誤差 ±0.05mm,合格尺寸范圍應在0.45~0.55mm之間,實測尺寸為0.5~0.547mm,僅占給定公差帶47%,如圖9所示。對腹板進行取點測量,測量結果如圖10所示,設計要求尺寸誤差0.5±0.05mm,測量尺寸0.46~0.539mm,占公差帶79%,表面粗糙度達到Ra1.6μm,滿足設計要求。
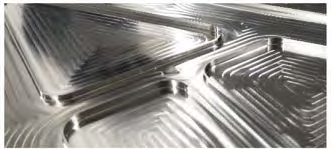
圖8 加工后的壁板
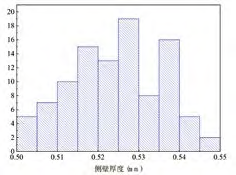
圖9 側壁厚度實測值分布圖
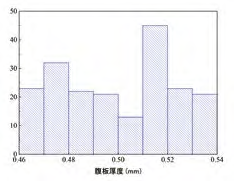
圖10 腹板厚度實測值分布圖
5、結論
本文針對鈦合金超薄壁板的加工難點問題進行了分析與試驗驗證,主要的工作有:
① 通過對直刃型立銑刀與螺旋型立銑刀的軸向切削力的差異進行了分析與試驗驗證,提出使用直刃型立銑刀進行精密加工工藝方案。利用直刃型立銑刀向下的軸向切削力避免腹板的過切,并且輔助壓緊零件。
② 利用余量加強剛度結構在加工中的剛度,結合切削試驗與有限元仿真,獲得適當的精加工余量。
③ 基于上述技術要點設計了鈦合金超薄壁板的精密加工工藝方案,在實際生產中取得了優秀的結果,零件腹板和側壁尺寸滿足設計需求±0.05mm公差范圍,零件粗糙度可達Ra1.6μm,滿足設計要求。以上工作為航空航天領域整體薄壁腹板類零件的加工提供了有益借鑒。
相關鏈接