引言
儲罐是石油石化行業(yè)重要基礎(chǔ)設(shè)施。我國已掌握10×104m3和15×104m3大型浮頂儲罐設(shè)計建設(shè)技術(shù),并成為石油儲備庫主要儲罐型式。大型儲罐如發(fā)生油品泄漏事故可能造成嚴重環(huán)境污染和經(jīng)濟損失。儲罐檢測是確定腐蝕狀態(tài)和減少風險隱患的可靠手段,通過分析儲罐腐蝕規(guī)律,驗證預測其工作性能和剩余壽命。儲罐檢測周期指從上一次檢測距離儲罐達到風險可接受標準的時間間隔,是儲罐進行維修的重要依據(jù)。
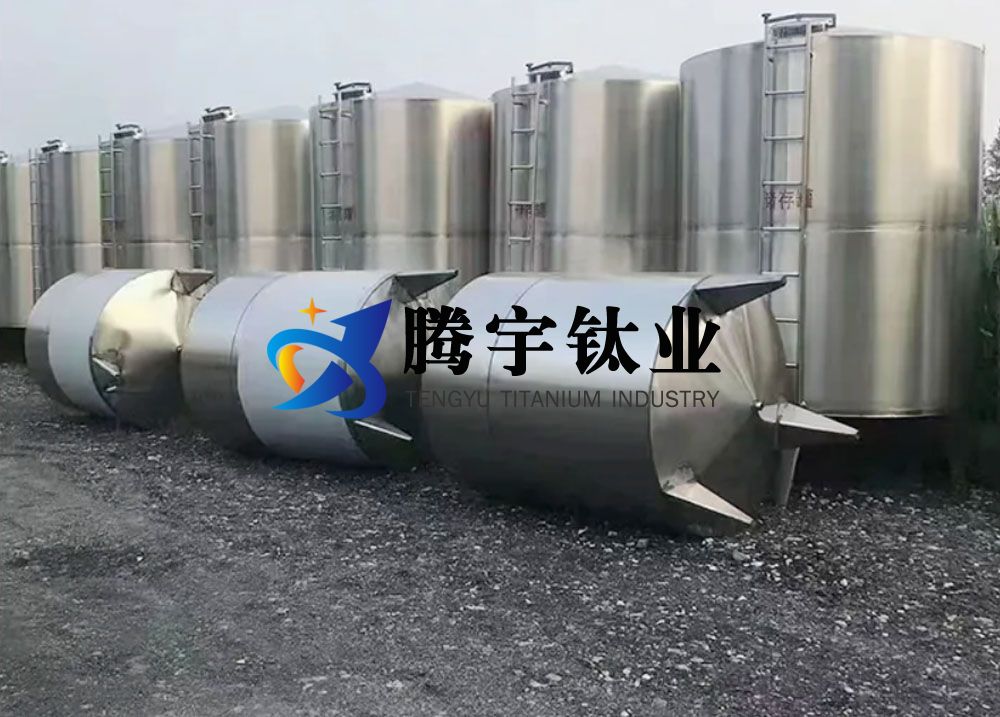
根據(jù)工程經(jīng)驗或相似案例的特定時間周期可能造成儲罐失修或過修。相比根據(jù)腐蝕速率、可靠性和極值分布理論等研究方法,提出基于風險的檢驗技術(shù)(Risk Based Inspection,RBI)的儲罐檢測周期,更適用于我國儲罐實際情況。確定科學合理的檢測周期,有利于減少檢驗維修費用、降低非計劃性停產(chǎn)損失,有效預防儲罐腐蝕穿孔泄漏事故,對于儲罐安全、高效和經(jīng)濟運行具有重要意義。
1、國內(nèi)外儲罐檢測標準規(guī)范
針對大型原油儲罐檢測周期,國內(nèi)標準存在不一致、不統(tǒng)一的情形。行業(yè)標準SY/T 5921-2017規(guī)定油罐檢測評價周期為5~8年,新建油罐第一次檢測評價周期不宜超過10年。
行業(yè)標準SY/T 6620-2014《油罐的檢驗、修理、改建及翻建》等同采用美國石油學會標準APIStd653-2009,規(guī)定儲罐檢測周期分為外部檢驗、超聲波厚度檢驗和內(nèi)部檢驗三種類型,儲罐檢測對應內(nèi)部檢驗情形。
(1)油罐外部檢驗周期應按照每5年和RCA/4N兩者的較短期限,RCA指測量的罐壁壁厚與要求的最小壁厚之差;N指罐壁腐蝕速率;
(2)超聲波厚度測量,如腐蝕速率未知,最大間隔時間為5年;如腐蝕速率已知,最大間隔時間是15年和RCA/2N兩者的較短期限;
(3)內(nèi)部檢驗指檢測罐底板腐蝕和滲漏。新建儲罐首次檢驗的周期不能超過10年,如儲罐底板厚度大于8mm且有陰極保護加玻璃纖維加強襯里,首次檢驗周期可延長至12~15年;如儲罐安裝滲漏防護和探測系統(tǒng),首次檢驗周期可延長至20~25年。
針對后續(xù)內(nèi)部檢驗時間間隔,根據(jù)獲取罐底板腐蝕速率和最小剩余厚度,最大時間間隔不超過20年,基于風險的檢驗評估(RBI),最大時間間隔不超過25年;如儲罐安裝滲漏防護和探測系統(tǒng),基于風險的檢驗評估(RBI),最大時間間隔不超過30年。
歐洲工程材料應用協(xié)會標準EEMUA 規(guī)定,潮濕地區(qū)原油儲罐檢測周期最長為8年;在溫暖干燥地區(qū)原油儲罐檢測周期最長為10年。
俄羅斯標準РД 153-39.4-056-2000 《干線輸油管道運行技術(shù)規(guī)程》規(guī)定儲罐設(shè)施附件專項檢測每5年不少于1次;全面檢測每10年1次,儲罐超出預期使用期限或已進行大修的儲罐檢測周期分別為4年和8年。
加拿大Enbridge公司采用API std 653標準規(guī)定的儲罐檢測時間間隔,最長可達20年。
可以看出API標準規(guī)定儲罐檢測周期較長,在儲罐狀況良好、施加陰極保護和泄漏監(jiān)測技術(shù)條件下,儲罐檢測周期超過20年。有學者認為,根據(jù)儲罐實際安全狀況確定檢測周期,大部分情形可以延長;國內(nèi)標準規(guī)定儲罐檢測周期較為保守,建議延長至8~10年。
2、儲罐檢測周期工程案例及做法
儲罐檢測涵蓋壁板/底板進行超聲波測厚、聲發(fā)射和無損檢測,以及儲罐基礎(chǔ)、焊縫、幾何尺寸和附件設(shè)施檢查。相對罐底板,罐壁板腐蝕相對輕微,罐底板油品滲漏風險遠高于罐壁油品泄漏風險。儲罐檢測盡可能減少不必要的無效檢測,檢測重點是罐底板、邊緣板、角焊縫和中央排水管等,儲罐檢測周期取決于罐底板使用壽命。
調(diào)研國內(nèi)油庫企業(yè)做法,根據(jù)儲罐實際情況采用固定時間的定期檢驗,存在下列問題:
(1)缺乏科學依據(jù)儲罐提前檢測,或者針對無嚴重缺陷儲罐開罐檢測,耗時長、費用高;影響正常生產(chǎn),造成不必要經(jīng)濟損失;
(2)儲罐存在較大風險隱患不能及時檢測,儲罐含風險隱患超期運行;
(3)固定時間的定期檢驗方式未考慮失效后果影響;缺乏靈活性,未考慮油庫企業(yè)管理水平差異化(管理水平較好可減少儲罐失效概率);
(4)固定時間的定期檢驗方式缺乏科學性,不能集中資源用于檢測風險等級較高的儲罐。
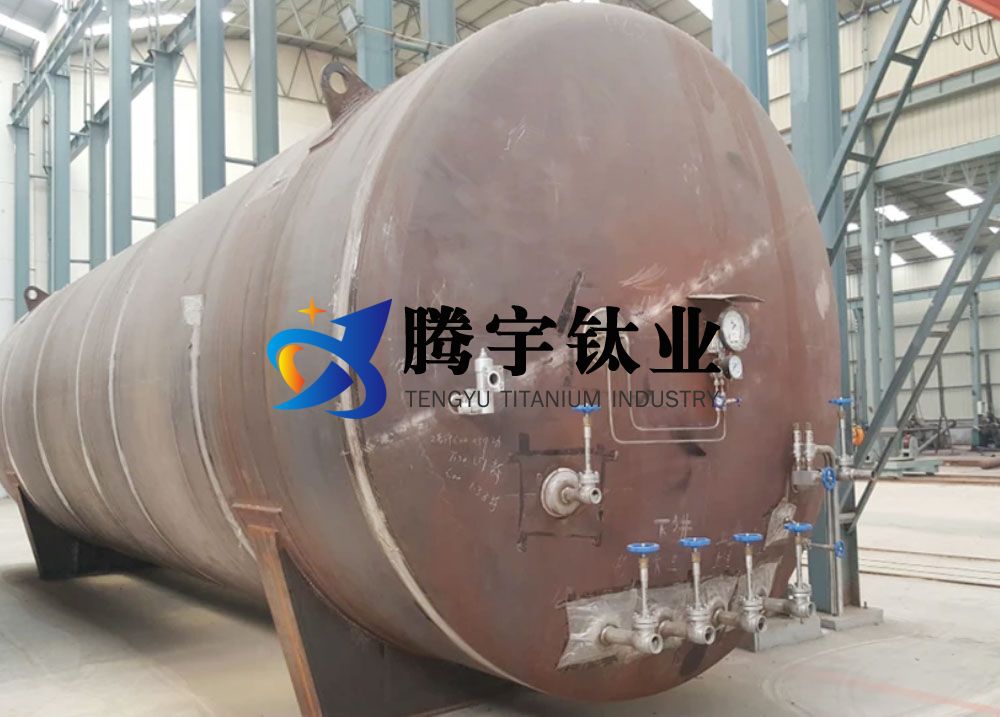
國內(nèi)西部石油儲備庫容量250×104m3,設(shè)計儲罐原油、柴油、汽油、航煤、燃料油儲罐50多座,因儲罐混摻中轉(zhuǎn)頻繁,儲罐長期連續(xù)運行,未進行全面系統(tǒng)檢測,針對原油儲罐開展完整性檢測評價,開展聲發(fā)射在線檢測和開罐無損檢測,罐底板漏磁檢測發(fā)現(xiàn)1處腐蝕深度超過設(shè)計厚度50%的缺陷,計算實際腐蝕速率進行風險評價,罐底板風險等級屬于中風險(3C),罐壁板風險等級屬于低風險(2B),風險評價預測儲罐檢測周期大于10年,最后綜合油庫實際狀況和經(jīng)濟分析、風險可接受標準確定檢測周期為9.6年。
3、儲罐檢測周期預測方法
國外推薦采用基于風險的檢驗技術(shù)(RBI)確定儲罐內(nèi)檢測周期,根據(jù)API 581進行風險評價等級排序,采取針對性風險緩解措施,制定儲罐整體檢測策略。我國安全行業(yè)標準AQ 3053-2015《立式圓筒形鋼制焊接儲罐安全技術(shù)規(guī)程》提出基于RBI的儲罐檢測周期。
3.1 RBI風險評價原理及技術(shù)路線
RBI是應用于設(shè)備維修管理技術(shù),基本思想是研究材料退化失效造成壓力設(shè)備介質(zhì)泄漏的風險,基于檢測結(jié)果實施風險控制。RBI指出風險是時間的函數(shù),表示為失效后果與失效概率的乘積。
Risk(t)=Pf (t).FC (1)
Pf (t)=gf .Df (t).FMS (2)
式中Pf (t)為失效概率;FC為失效后果,指環(huán)境損失后果和經(jīng)濟損失后果,包括環(huán)境罰款、處置費、維修費和停產(chǎn)經(jīng)濟損失等;gf 指設(shè)備平均失效頻率,通過設(shè)備歷史統(tǒng)計數(shù)據(jù)得到;Df (t)為破壞因子,表征不同失效機理對設(shè)備的影響程度,儲罐考慮腐蝕壁厚減薄和內(nèi)襯損壞兩種失效機理;FMS為管理因子,表示設(shè)備安全管理對風險影響。
基于RBI技術(shù)的儲罐檢測周期研究方法是根據(jù)檢測結(jié)果和工程經(jīng)驗預估下次檢測間隔,根據(jù)RBI技術(shù)計算下次檢測時的風險值,與儲罐可接受風險值比較,增加或減少檢測間隔直至二者相等,即確定為儲罐下次檢測周期。RBI失效后果計算模型中只考慮油品泄漏風險,未考慮儲罐火災爆炸、人員中毒傷亡等后果類型,這類事故危害程度嚴重,因此應進一步研究儲罐風險評價方法。
3.2 儲罐可接受風險
儲罐可接受風險水平是決定基于RBI技術(shù)的儲罐檢測周期的關(guān)鍵因素。如可接受風險值過高,儲罐在高風險條件下運行,可能導致泄漏失效;可接受風險值過低,儲罐檢測周期過短,增加運行和檢測成本。可接受風險值原則是保證儲罐安全運行條件下盡可能延長儲罐檢測周期,可認為儲罐可接受風險為儲罐底板被腐蝕至最小允許厚度對應的風險值。
API Std653-2009規(guī)定儲罐未安裝滲漏防護和探測系統(tǒng),罐底板最小允許厚度為2.54mm,如未安裝滲漏防護和探測系統(tǒng),罐底板最小允許厚度為1.27mm。調(diào)研國內(nèi)儲罐設(shè)計做法,取值2.54mm。以10×104m3和5×104m3儲罐為例,儲罐可接受風險值約為3.6×104。文獻[A]指出大型常壓儲罐的最大可接受破壞因子取值300。
3.3 計算示例
某油庫建有大型原油儲罐38座,主要型式為10×104m3和5×104m3浮頂儲罐,針對19座儲罐進行開罐檢測,罐底板進行100%漏磁檢測。儲罐可接受風險3.6×104,結(jié)論是除2#、5#和10#儲罐檢測周期為8年、11年和11年,其他儲罐檢測周期均大于12年,基于RBI技術(shù)預測儲罐檢測周期均大于8年,證明國內(nèi)標準SY/T 5921規(guī)定的儲罐檢測周期較為保守。
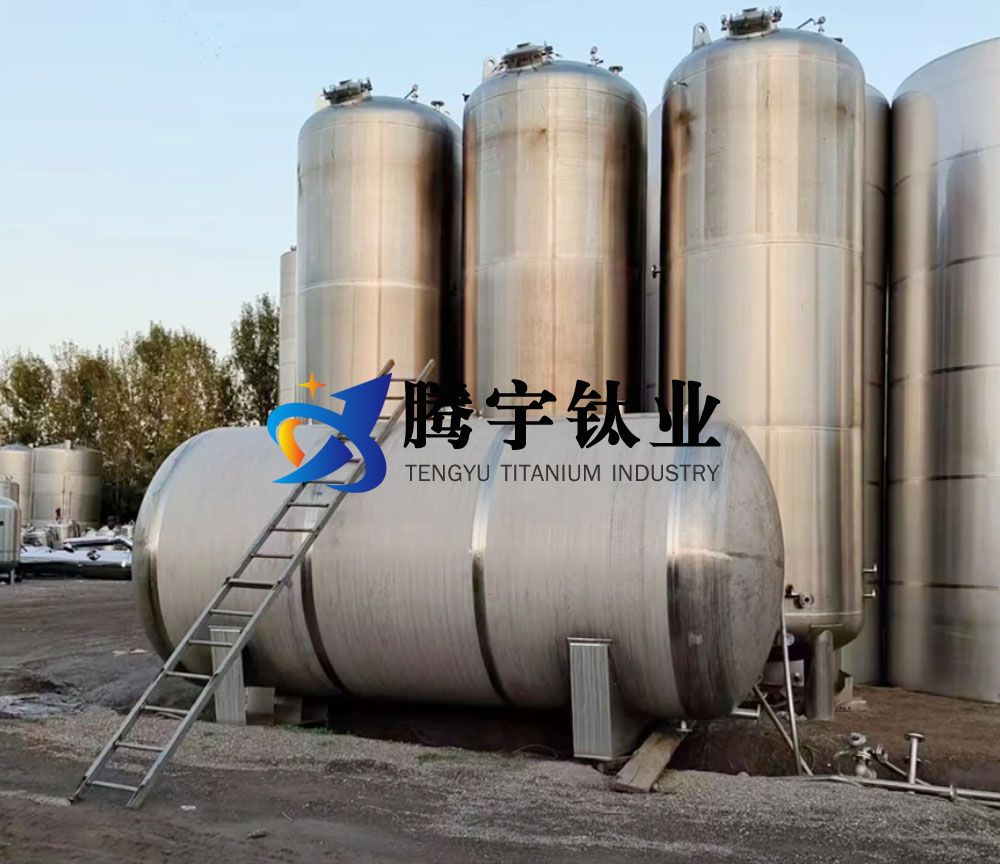
4、結(jié)語
行業(yè)標準SY/T 5921-2017關(guān)于儲罐內(nèi)檢測周期較為保守,會增加油庫運行和維修成本。基于RBI技術(shù)是根據(jù)罐底板厚度、腐蝕速率、最小允許厚度和可接受風險確定儲罐檢測周期,該方法預測儲罐檢測周期較為合理、準確。建議采用基于RBI技術(shù)確定儲罐檢測周期,考慮儲罐實際風險水平與企業(yè)風險可接受水平,綜合分析風險等級及驅(qū)動機理、儲罐運行歷史、檢測數(shù)量及有效性以及類似案例等,適當延遲儲罐檢測周期。
參考文獻
[1] 鄧霄, 白天陽, 崔宇翔. 含腐蝕缺陷管道剩余壽命預測方法評述[J]. 油氣與新能源, 2021, 33(4): 28-32.
[2] 馬偉平, 張帆, 房偉. 高鋼級管道切割技術(shù)現(xiàn)狀綜述. 油氣與新能源, 2022, 34(6): 77-81.
相關(guān)鏈接