由于鈦材焊接性問(wèn)題,在鈦材設(shè)備制造過(guò)程中需采取一些特殊工藝措施與技術(shù)手段,才能保證質(zhì)量。本文結(jié)合騰宇鈦業(yè)鈦列管式換熱器、鈦儲(chǔ)罐、鈦反應(yīng)釜、鈦分離器等設(shè)備制作實(shí)踐予以介紹。
一、焊接缺陷及原因
鈦材設(shè)備在焊接時(shí)極易氧化、氮化和脆裂。鈦不僅在熔融狀態(tài)下能和幾乎所有元素起作用,而且在350~400℃時(shí)即開(kāi)始大量吸氫。氫是鈦中最有害的元素之一,它能降低鈦的塑性與韌性,導(dǎo)致脆裂。當(dāng)冷卻時(shí),氫來(lái)不及逸出而聚成氣孔。故一般要求鈦中含氫量在0.01%以下。若母材或焊接材料中含氫量大,則應(yīng)預(yù)先作脫氫處理。鈦在600℃以上就會(huì)急劇地和氧、氮化合,生成二氧化鈦和氮化鈦(硬度極大),當(dāng)加熱到800℃以上,二氧化鈦即溶解于鈦中并擴(kuò)散深入到金屬鈦的內(nèi)部組織中去,形成0.01~0.08mm的中間脆性層。溫度越高,時(shí)間越長(zhǎng),氧化、氮化也越嚴(yán)重,焊接接頭的塑性就急劇降低。為此,一般要求鈦中含氧量應(yīng)在0.1%以?xún)?nèi)。此外,鈦還易與碳形成脆性的碳化物,降低塑性和可焊性。

鈦易過(guò)熱。鈦的熔點(diǎn)高(1680~1725℃),屬難熔金屬,在焊接時(shí)需要高溫?zé)嵩础b伒膶?dǎo)熱系數(shù)低,僅為碳鋼的一半,熱量不易散失,過(guò)熱傾向嚴(yán)重。鈦在885℃時(shí)產(chǎn)生同素異構(gòu)轉(zhuǎn)變,由α鈦(密集六方晶格)轉(zhuǎn)變?yōu)棣骡?體心立方晶格),溫度再高,盧鈦的晶粒便會(huì)急劇地跳躍式地長(zhǎng)大,使性能迅速變壞。當(dāng)結(jié)構(gòu)剛性大時(shí),焊接拉應(yīng)力作用,還會(huì)導(dǎo)致產(chǎn)生裂紋。
此外,鈦一旦沾染鐵離子即變脆。這也是導(dǎo)致鈦材產(chǎn)生焊接裂紋的重要原因之一。
二、主要工藝措施及控制
1、生產(chǎn)準(zhǔn)備工作
1)施工場(chǎng)地及其要求
鈦材焊接應(yīng)在獨(dú)立的鈦加工車(chē)間進(jìn)行。如果在鋼鐵車(chē)間內(nèi)進(jìn)行焊接,應(yīng)與作業(yè)區(qū)隔開(kāi)。鈦材焊接應(yīng)遠(yuǎn)離通風(fēng)口和敞開(kāi)的門(mén)窗處,焊接作業(yè)處風(fēng)速<10m/s,相對(duì)濕度<90%。若條件許可,在鈦材焊接場(chǎng)地鋪設(shè)地面,禁止鐵污染,搭防塵棚,配備去濕機(jī),對(duì)提高焊接質(zhì)量有良好效果。
2)簡(jiǎn)體與零部件的下料
鈦材與不銹鋼、鋁材一樣,表面不得有硬印標(biāo)記(樣沖孔等),應(yīng)用鉛筆(色筆)劃線(xiàn)。鈦薄板可以剪切下料,厚板可用氧乙炔焰或等離子弧切割。切口要留加工余量,用機(jī)械方法去除表面污染層。為了防止在各道工序受到損壞,表面應(yīng)貼牛皮紙保護(hù)。鈦表面打磨只能用橡膠或尼龍滲合氧化鋁的砂輪,絕不能用打磨過(guò)碳鋼的砂輪。打磨時(shí)不允許出現(xiàn)過(guò)熱的色澤。
3)板坯的坡口加工與卷圓
縱縫坡口用刨邊機(jī)加工,坡口加工后卷圓,以免錯(cuò)邊。卷板機(jī)滾筒表面應(yīng)清理干凈。由于鈦的彈性模量較低,回彈量大,可采用模壓法(預(yù)彎)或在三輥卷板機(jī)上模板滾壓成型。要認(rèn)真對(duì)待和嚴(yán)控簡(jiǎn)體縱縫棱角度。
4)管板的管孔加工
這是換熱器制造的主要環(huán)節(jié)之一。鈦比不銹鋼有更大的咬粘傾向,管孔加工要用短而銳利的鉆頭,慢速、強(qiáng)制進(jìn)給,用堅(jiān)固支架,使其利于排屑;而且宜用大量、足夠的冷卻潤(rùn)滑液。根據(jù)經(jīng)驗(yàn),采用鉆孔一擴(kuò)孔成形工藝或鉆孔一鉸孔成形工藝效果較好。
5)管子與管板的連接
鈦管與管板接頭一般采用貼脹后焊接。貼脹脹緊率一般控制在3%~5%。鈦的加工性能較差,變形速率敏感性高,為避免脹接時(shí)產(chǎn)生裂紋,應(yīng)由專(zhuān)用脹接工具慢速進(jìn)行。
6)封頭的壓制
用煤氣爐加熱坯料到300~500℃,經(jīng)多次壓制成形。對(duì)于薄壁封頭,亦可采用夾板拉深法(沖壓機(jī)上壓制)。這種方法是將薄板料夾在兩塊較厚的板料中間,并將周?chē)杆篮罄睢3尚秃髮⒑缸〉牟课桓畹簦〕鰥A在中間的所需封頭(此法可避免鼓包與皺褶等缺陷)。
2、簡(jiǎn)體主焊縫(縱向與環(huán)向焊縫)焊接工藝
鈦設(shè)備主焊縫可選用表1所述的焊接方法。鈦的等離子弧焊近年來(lái)得到廣泛應(yīng)用,一般采用小孔法焊接。附加保護(hù)氣及背面保護(hù)氣都應(yīng)制作專(zhuān)門(mén)的氣罩,緊密地與等離子噴嘴連結(jié),又要與其絕緣。對(duì)于厚度3~4mm鈦板,專(zhuān)門(mén)氣罩的長(zhǎng)度應(yīng)大于120mm。
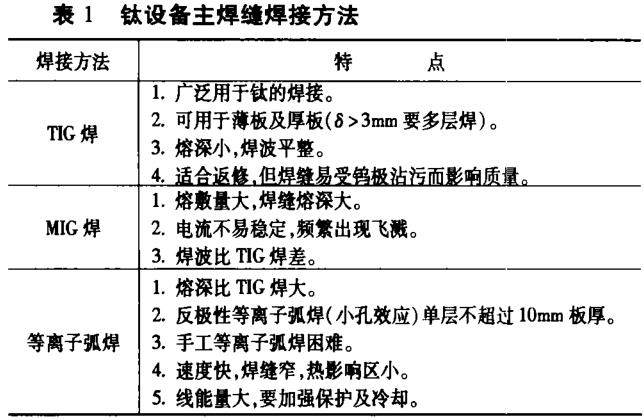
TIG焊用得最廣,除手工外,也可以側(cè)面送絲進(jìn)行自動(dòng)焊接(小車(chē)行走,轉(zhuǎn)胎轉(zhuǎn)動(dòng)),還可以加脈沖電源進(jìn)行自動(dòng)焊接。表2是蒸發(fā)器67m2TA2工業(yè)純鈦簡(jiǎn)體縱、環(huán)縫用側(cè)面送絲自動(dòng)TIG焊的工藝參數(shù),鈦板厚8mm。焊前坡口用不銹鋼絲刷及丙酮清理,焊絲也經(jīng)清理。第1層采用手工焊是考慮裝配錯(cuò)邊時(shí)容易控制;第5層因在簡(jiǎn)體內(nèi)部,焊機(jī)頭難進(jìn)入,故也用手工焊。除第5層外,用φ2mmTA2鈦絲作填充絲。鎢極直徑4mm。氬氣純度99.99%以上,主流量14~15L/min,尾罩氣流量15~20L/min,背面保護(hù)氣流量10~15L/min。
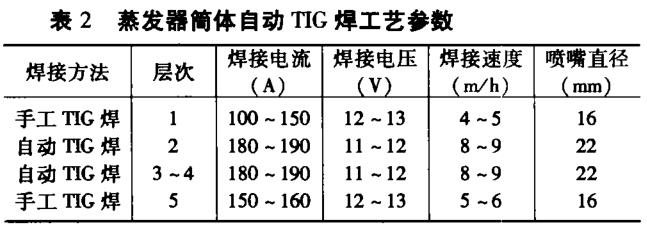
焊好鈦設(shè)備縱、環(huán)縫的關(guān)鍵是氬氣保護(hù),尾罩及背面保護(hù)氣罩必須設(shè)計(jì)并安置好,最難的是背面保護(hù),切要小心從事。
3、鈦管與鈦管板焊接
鈦管與鈦管板焊接有先脹后焊和只焊不脹兩種。前者多用于鈦復(fù)合鋼管板,后者用于全鈦材管板。當(dāng)設(shè)備小、壓力與溫度較低、受力不大而管板較薄時(shí),一般用全鈦材作管板,此時(shí)管子與管板只焊不脹。
1)焊接方法與氬氣保護(hù)
管端焊口可采用手工鎢極氬弧焊配以特制的保護(hù)氣罩進(jìn)行焊接。或采用微機(jī)控制的自動(dòng)脈沖TIG焊(加絲或不加絲)。
應(yīng)特別重視氬氣保護(hù)。因鈦在350~C以上時(shí)會(huì)強(qiáng)烈吸氣、脆化,引起氣孔及裂紋,焊接時(shí)必須將焊接接頭及附近區(qū)域溫度維護(hù)至200~C。
2)焊接工藝與控制
焊前要檢查管板孔、管徑及中心距尺寸(傳熱管應(yīng)倒內(nèi)角0.5×45°),管子凸出管板尺寸要盡量一致,由專(zhuān)用工具檢查。如需脹管,脹管前管端與管板間隙應(yīng)<0.5mm,脹管后管壁內(nèi)50mm范圍內(nèi)管板表面用丙酮去油,用無(wú)鐵砂紙磨去氧化膜,顯出金屬光澤。
焊接時(shí)宜安排好合理的順序。以管板中心為基準(zhǔn),兼顧各個(gè)方向劃分幾個(gè)區(qū)域,然后按分區(qū)(由中心向四周幅向向外地焊接,并盡量注意各向的對(duì)稱(chēng)性與平衡性)進(jìn)行焊接。這樣管板不易因焊接而發(fā)生凸起或凹進(jìn)變形。
焊接工藝參數(shù)因焊接方法不同而異。TIG焊可參照縱、環(huán)縫手工TIG焊。微機(jī)控制的脈沖TIG時(shí),如線(xiàn)能量小,則冷卻快,會(huì)出現(xiàn)鈦馬氏體(α'相),塑性下降;如線(xiàn)能量大,則冷卻慢,晶粒會(huì)長(zhǎng)大,塑性也降低。
故線(xiàn)能量一般取6kJ/cm~8kJ/cm為妥,此外,線(xiàn)能量再小則管板接頭熔深太淺,難以達(dá)到質(zhì)量要求。
焊接管板接頭時(shí),如焊后顏色不為銀白色及金黃色,應(yīng)磨去,重焊。如出現(xiàn)氣孔、裂紋,須磨去重焊。
三、注意事項(xiàng)
采用鎢極氬弧焊時(shí),還需注意以下幾點(diǎn)。
1、焊前預(yù)先通氣一段時(shí)間,而后再起弧焊接。
2、采用較大口徑的噴嘴時(shí),噴嘴與工件的距離適當(dāng)縮小以加強(qiáng)保護(hù)。鎢極伸出噴嘴的長(zhǎng)度宜短,以不妨礙觀察到熔池為限。
3、采用短弧焊效果好,勿擺動(dòng)焊槍。
4、焊絲熱端在焊接過(guò)程中不能脫離保護(hù)范圍,如發(fā)現(xiàn)被氧化,須將氧化部分切去才能繼續(xù)使用。
5、焊接結(jié)束時(shí)要滯后停氣,直至焊接區(qū)溫度降至材質(zhì)穩(wěn)定的范圍,一般溫度在200~C以下。
6、如某部分焊縫保護(hù)不好,焊道表面發(fā)生氧化,須將氧化皮去除后才能進(jìn)行下一道焊接。
7、焊接簡(jiǎn)體環(huán)縫時(shí),內(nèi)襯銅墊環(huán),可起到撐圓的作用。
8、焊后熱處理。根據(jù)鈦材成分和結(jié)構(gòu)使用要求可選用退火、時(shí)效或淬火一時(shí)效處理(宜嚴(yán)格按規(guī)范進(jìn)行)。
相關(guān)鏈接