繞管式換熱器作為全球大型液化天然氣工廠的主低溫換熱器[1],其單線生產(chǎn)能力可達780×105t/a。液化天然氣(LNG)繞管式換熱器技術(shù)門檻極高,殼側(cè)工質(zhì)為氣液兩相時,氣液相之間的相互作用使得殼側(cè)傳熱與壓降計算變得復(fù)雜。因此,需要針對殼側(cè)大質(zhì)流密度下的相變流動進行研究,為繞管式換熱器的設(shè)計與優(yōu)化提供理論依據(jù)。由于繞管式換熱器造價昂貴,目前其實驗研究較少,國內(nèi)外課題組多通過工程計算和數(shù)值模擬的方法進行設(shè)計分析。歐陽新萍等[2]提出了兩種用于工程計算的方法,將多股流繞管式換熱器的計算分解為單股流,簡化了計算過程。Li等[3]建立了晃蕩工況下的繞管式換熱器數(shù)值模型,研究表明橫搖和縱搖均會導(dǎo)致傳熱惡化。邱國棟等[4]建立了丙烷在管側(cè)進行冷凝換熱的數(shù)值模型,結(jié)果表明傳熱系數(shù)隨質(zhì)量流率的增加而增加。吳志勇等[5]對繞管式換熱器殼側(cè)沸騰過程進行了數(shù)值研究,結(jié)果表明,工質(zhì)為乙烷與丙烷時,時間松弛參數(shù)為3s-1。王斯民等[6]提出了一種通過安裝直插式墊條型內(nèi)插件來增強繞管式換熱器換熱性能的方案,并通過數(shù)值模擬研究了其流動換熱性能,結(jié)果表明此方案能將綜合換熱性能提高7.4%~10.5%。楊發(fā)煒等[7]通過流場模擬軟件研究了管徑和層間距對繞管式換熱器殼程換熱性能的影響,結(jié)果表明,換熱器的換熱效果隨層間距的增大而減小,且并管換熱系數(shù)在流速較高時高于非并管。He等[8]通過改變幾何模型的纏繞角,使用數(shù)值計算的方法研究了不同模型下纏繞管式換熱器殼程流動換熱規(guī)律,發(fā)現(xiàn)殼側(cè)局部換熱系數(shù)分布與膜厚分布一致,平均換熱系數(shù)隨雷諾數(shù)增加而增加,隨纏繞角度增加而減小。馬飛[9]提出了一種纏繞管式換熱器殼側(cè)多目標驅(qū)動優(yōu)化遺傳算法以及殼程努塞爾數(shù)和阻力系數(shù)之間的關(guān)聯(lián)關(guān)系。在實驗研究方面,汪耀龍等[10]設(shè)計了一種均布器,以水為工質(zhì)進行了流體均布特性研究,結(jié)果表明設(shè)置均布器對液相流體的均布性能有所提升。
Neeraas等[11-12]設(shè)計了一種用于研究單相工質(zhì)在殼側(cè)傳熱流動的小型實驗系統(tǒng),開發(fā)了殼側(cè)氣相與液相工質(zhì)下的傳熱和壓降關(guān)聯(lián)式。Sun等[13]設(shè)計了一種雙混合制冷劑實驗裝置,研究了復(fù)合晃蕩情況下繞管式換熱器殼側(cè)流動情況,結(jié)果表明殼側(cè)壓降受晃蕩影響大于溫度影響。Hu等[14]設(shè)計了一種低溫實驗平臺,研究了小質(zhì)流密度下傳熱系數(shù)隨干度的變化規(guī)律,結(jié)果表明傳熱系數(shù)隨干度先增加后減小。李豐志等[1]設(shè)計了一種管側(cè)低溫實驗系統(tǒng),以液相丙烷為工質(zhì)進行了實測,得到了較高精度的實驗數(shù)據(jù)。龐曉冬等[15]設(shè)計了一種螺旋折流板管殼式換熱器實驗系統(tǒng),研究了丙烷在管側(cè)的冷凝換熱特性,結(jié)果表明,在干度0.9時,換熱系數(shù)達到峰值。
Zhu等[16]設(shè)計了一種浮式液化天然氣實驗裝置,測試原料氣流量和海況對繞管式換熱器的適應(yīng)性,結(jié)果表明,當(dāng)原料氣完全液化時,降溫速率逐漸增大。Sun等[17]通過一種低溫工質(zhì)晃蕩實驗裝置,對海上液化天然氣產(chǎn)業(yè)鏈主低溫換熱器多相流動特性進行了研究,提出當(dāng)蓋板的防晃動角度為15°時,液體波動指數(shù)較小,抗晃動性能良好。Zheng等[18]建立了以水和空氣為介質(zhì)的實驗測試系統(tǒng),研究了螺旋管換熱器殼程氣液混合物的分配性能,結(jié)果表明,當(dāng)氣體含量為0.4左右時,管式分布器具有較好的兩相均勻性。綜上所述,現(xiàn)有研究多集中于工程計算和模擬研究,獲得了一系列有益的結(jié)果。但是已有研究主要集中于單相工況及管側(cè)研究,對于換熱器殼側(cè)的實際低溫混合工質(zhì)兩相流動、沸騰相變及其對壓降和傳熱側(cè)影響研究還較少且缺少實驗驗證。因此,本文針對烴類工質(zhì)在殼側(cè)的兩相流動及傳熱、壓降特性問題,結(jié)合數(shù)值模型和實驗研究了干度、熱流密度、質(zhì)流密度等參數(shù)對繞管式換熱器傳熱、壓降及流型變化的影響。
1、模型構(gòu)建
1.1繞管換熱器物理模型
工業(yè)中繞管式換熱器具體結(jié)構(gòu)如圖1所示。其工作原理為低溫的混合烷烴制冷劑以噴淋形式由上而下地從殼側(cè)流過,而溫度較高的天然氣從管側(cè)自下而上地流動,兩者通過繞管壁面發(fā)生換熱,混合烷烴吸熱汽化,而天然氣放熱降溫實現(xiàn)液化[19-20]。由于繞管式換熱器結(jié)構(gòu)龐大,其管束排列復(fù)雜,若將整個繞管式換熱器作為模擬對象,計算時間將大幅增加且難以收斂。而選擇合適的尺寸來簡化模型能在更少的計算時間內(nèi)有效提高計算精度。本文選取繞管式換熱器尺寸的八十分之一(θ=4.5°)為研究對象。
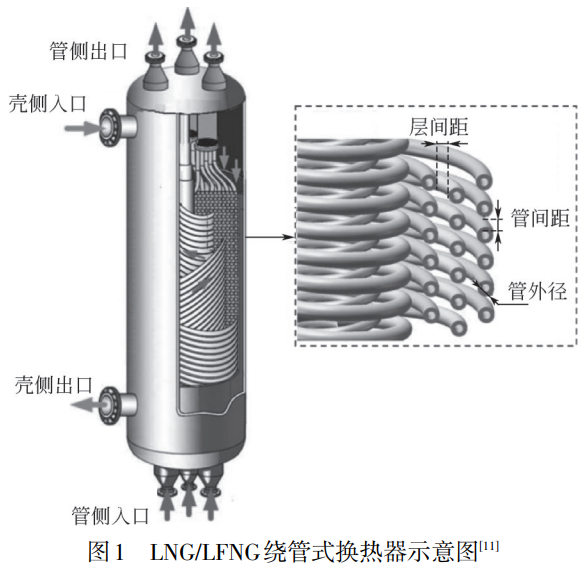
根據(jù)董龍飛等[21]的研究,流通長度上的簡化帶來的誤差遠小于流動波動帶來的誤差。Li等[3]的模擬研究表明,該軸向長度既不會過短而造成偏離實際繞環(huán)結(jié)構(gòu)的叉排效果,也不會因為過長而浪費計算資源。模型的具體參數(shù)如圖2所示。幾何模型由5列繞管組成,其中左右兩列為半圓管緊貼壁面,具體結(jié)構(gòu)如圖1所示。氣液兩相的混合烷烴通過頂部直徑為8mm的噴淋孔進入殼側(cè)。換熱測試段中通過給定熱流密度的方式來研究換熱器殼側(cè)傳熱特性,為模擬不銹鋼繞管在傳熱中的效果,在傳熱測試段內(nèi)增加6mm壁厚的固體域。殼側(cè)幾何模型的主要參數(shù)為:繞管外徑12mm,繞管內(nèi)徑6mm,管間距(橫向管間)2mm,層間距(縱向剖層間)1mm,螺旋升角4°,繞管長度200mm。
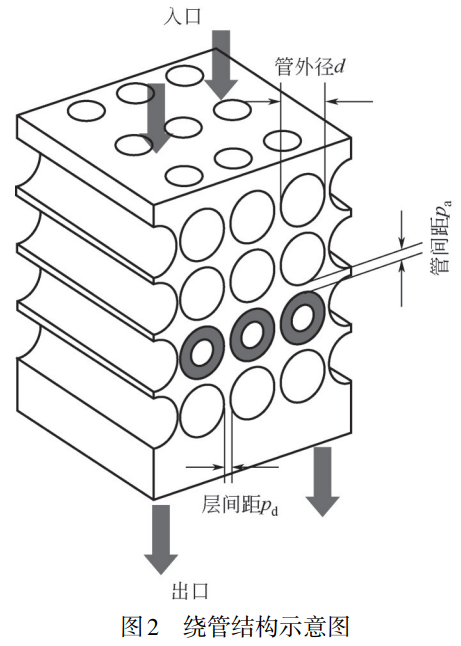
1.2數(shù)值模型
纏繞管換熱器中殼側(cè)制冷劑的相變是一個降膜沸騰過程,包括管壁上液相的蒸發(fā)和兩個相交界面之間的傳質(zhì)。工作介質(zhì)的流動主要受重力、摩擦力和表面張力的影響。根據(jù)濕度測量結(jié)果[22],假設(shè)工作介質(zhì)與管壁之間的接觸角為10°。獲得殼側(cè)準確傳熱特性的關(guān)鍵是建立合理的傳質(zhì)模型、接觸角模型和潛熱模型,模擬殼側(cè)工作介質(zhì)在纏繞管換熱器中的傳熱傳質(zhì)過程。該模型的具體邊界條件為:入口采用指定質(zhì)流密度入口,出口自由流出,固體域內(nèi)壁面為定熱流密度壁面,其余壁面均為靜止、無滑移的絕熱壁面,考慮重力影響,流量為9.81m2/s,方向垂直向下。基于N-S方程,針對降膜蒸發(fā)模型選用式(1)~式(8)控制方程。
連續(xù)性方程
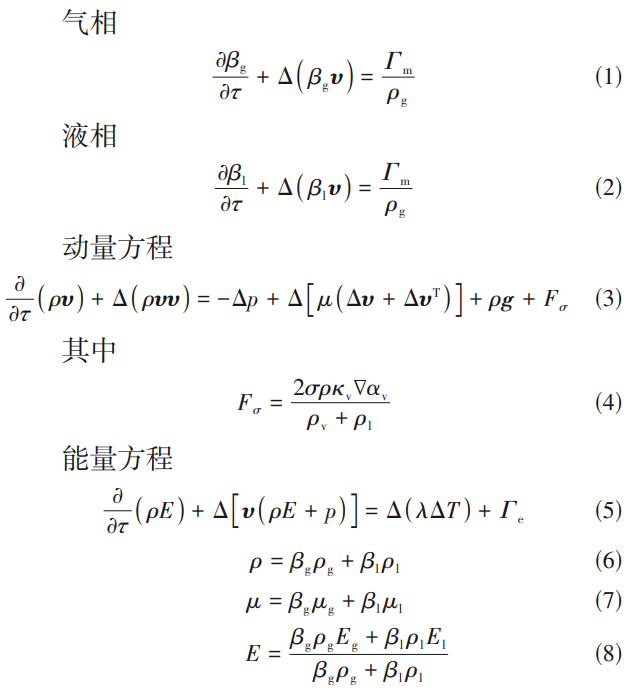
式中,τ為時間,s;p為壓力,MPa;μ為黏度,mPa.s;g為重力加速度,m/s2;ρ為密度,kg/m3;Fσ為相間作用力,N;σ為界面張力,N;κv為界面曲率;αv為體積分數(shù);ρv為氣相密度,kg/m3;ΔT為溫差,K;μg為氣相速度,m/s;μl為液相速度,m/s;ρg為氣相密度,kg/m3;ρl為液相密度,kg/m3;βg為汽相體積分數(shù);βl為液相體積分數(shù);v為汽相和液相的共享速度(矢量),m/s;E為內(nèi)能;E1為液相內(nèi)能,J;Γm為連續(xù)方程的源項;Γe為能量方程的源項。殼側(cè)沸騰過程中質(zhì)量與能量的傳輸通過以下模型進行描述。(1)相變傳質(zhì)模型傳質(zhì)源項分為蒸發(fā)和冷凝兩部分進行考慮,根據(jù)Lee模型,當(dāng)工質(zhì)的局部溫度高于飽和溫度即T≥Tsat時,發(fā)生蒸發(fā),并且控制單元內(nèi)液相轉(zhuǎn)變?yōu)槠嗟钠縨lv[式(9)]。

反之,若工質(zhì)的局部溫度低于飽和溫度即T<Tsat時,發(fā)生冷凝,并且控制單元內(nèi)汽相轉(zhuǎn)變?yōu)橐合嗟钠縨vl[式(10)]。

式中,coeff為時間松弛參數(shù),根據(jù)吳志勇等[5]的研究取值為3s-1。(2)潛熱傳熱模型相變過程中的熱量傳輸是通過連續(xù)方程中添加潛熱傳熱源項Γe實現(xiàn)的,Γe可用式(11)表達。

式中,hLH為工質(zhì)的汽化潛熱,J/kg。模型采用三維雙精度計算器,選取壓力基求解器,采用穩(wěn)態(tài)二階隱式計算,啟用能量方程,湍流模型選取RNGk-ε模型,使用VOF多相流模型,壁面附近流動采用標準壁面函數(shù),壓力速度耦合采用SIMPLEC算法,梯度離散采用Green-GaussNodeBased離散格式,壓力基采用PRESTO,其余離散均采用二階迎風(fēng)離散格式。數(shù)值模擬中以0.45∶0.55(本文所有組分比例均為摩爾比)的乙烷和丙烷(C2/C3)為工質(zhì)。其熱物性如密度、比熱容等采用了陳永東等[23]對混合介質(zhì)熱物性的計算方法。
1.3測試通道流通面積
為準確輸入模型入口處的質(zhì)流密度,殼側(cè)流通處的橫截面積計算就尤為重要。Fredheim[24]通過對繞管間的層間距積分導(dǎo)出換熱器殼側(cè)的平均流通橫截面積。本文采用該方法對殼側(cè)制冷劑的流通面積進行計算,如式(12)。

式中,S為殼側(cè)流通面積,m2;D為總寬度,m;dd為徑向管中心距,m;dg為氣相殼側(cè)平均流動間隙,m,計算如式(13)。
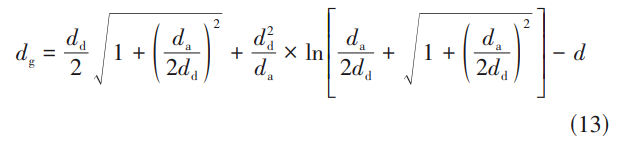
2、驗證實驗
近期,國際國內(nèi)繞管式換熱器方面的最新研究較少且主要的經(jīng)典關(guān)聯(lián)式年代較為久遠,因此搭建了以浮式液化天然氣(FLNG)/LNG繞管式換熱器為測試件的大質(zhì)流密度混合工質(zhì)流動傳熱測試的實驗系統(tǒng),可以實現(xiàn)對低溫條件下繞管式換熱器殼側(cè)流動換熱特性研究。本實驗系統(tǒng)包括主循環(huán)回路、冷卻回路、控制系統(tǒng)等。主要設(shè)備包括壓縮機、冷卻塔、換熱器、冷水機組、冷凍機組、冷水機組換熱器、冷凍機組換熱器、液氮換熱器(微通道換熱器)、氣動開關(guān)閥、氣動調(diào)節(jié)閥、干度調(diào)節(jié)電加熱器、過熱電加熱器、緩沖罐,如圖3所示。管程換熱采用模擬加熱管束實現(xiàn)。實驗過程中,乙烷工質(zhì)與丙烷工質(zhì)按各自質(zhì)量比分別進行充注,實驗系統(tǒng)中,壓縮機入口處及流量計入口處各布置有一個實驗工質(zhì)取樣口,分別對氣相及液相工質(zhì)進行取樣。實驗系統(tǒng)穩(wěn)定后,分別從兩個取樣口對工質(zhì)取樣,并通過氣相色譜儀對取樣樣本進行色譜分析。當(dāng)氣相取樣口與液相取樣口得到的樣本中各組分摩爾分數(shù)偏差小于1%時,認為實驗系統(tǒng)運行穩(wěn)定且取樣有效。本文研究中涉及的物性參數(shù)通過GERG-2004天然氣混合物物性模型[25]計算得到。
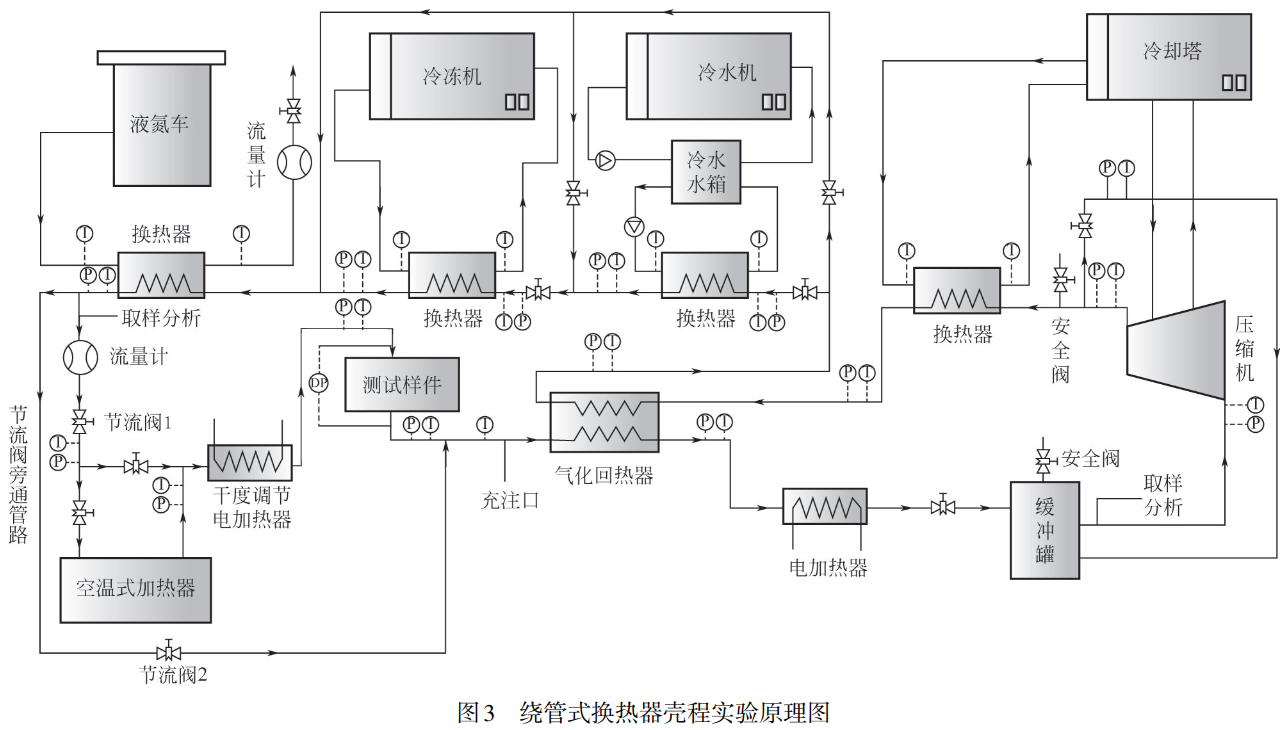
如圖4所示,本實驗平臺選取與實際應(yīng)用相貼近的結(jié)構(gòu)尺寸參數(shù),其中層間距為1mm,管間距為2mm,管外徑為12mm,管內(nèi)徑為6mm,螺旋升角為4°,與數(shù)值模型一致。測試件從上至下依次為入口段、均流穩(wěn)流段、壓降測試段、傳熱測試段、觀察窗以及測試樣件出口段。數(shù)值模型中也采用了和實驗?zāi)P鸵恢碌膫鳠岷蛪航当O(jiān)測段。此外,在測試件入口處還采用了多孔均流板,以實現(xiàn)流體均勻分布。實驗工質(zhì)為摩爾比0.45∶0.55的乙烷和丙烷。實驗采用的所有熱電偶均在-196~50℃溫度范圍內(nèi)進行了標定,并在傳熱系數(shù)計算過程中對各溫度數(shù)據(jù)進行修正。本實驗針對壓降測量在測試樣件上布置的測點包括壓差引壓測點和壓力引壓測點,傳感器布置時已避免測點探頭對測試樣件內(nèi)部流動特征產(chǎn)生明顯影響。壓力引壓測點布置在壓降測試段入口處,壓差引壓測點布置在壓降測試段入口和出口處,壓力和壓差引壓測點不會占據(jù)內(nèi)部流體通道,因此不會對測試樣件內(nèi)部流動產(chǎn)生明顯影響。
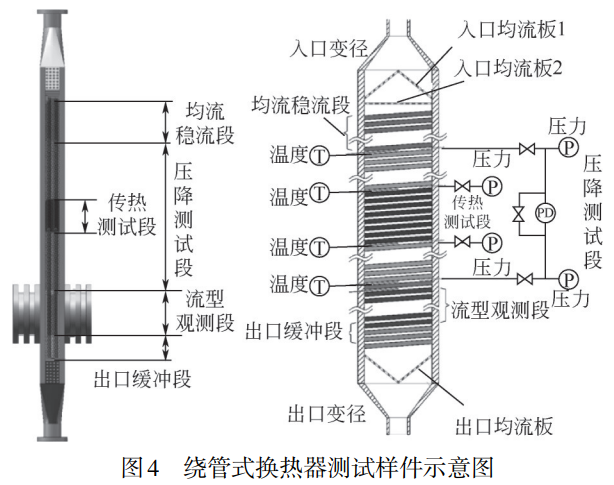
實驗系統(tǒng)整體采用一層二烯烴和兩層橡塑的方案進行保冷,經(jīng)熱平衡測算,系統(tǒng)漏熱造成的工質(zhì)干度變化小于0.01,可認為實驗系統(tǒng)為絕熱條件。特別地,傳熱流動核心部件測試樣件部分,漏熱率小于0.31%,可以認為實驗測試樣件部分漏熱防護良好。實驗系統(tǒng)的傳熱系數(shù)主要由熱流密度、管壁溫度與流體溫度計算得到,計算公式如式(14)~式(17)所示。
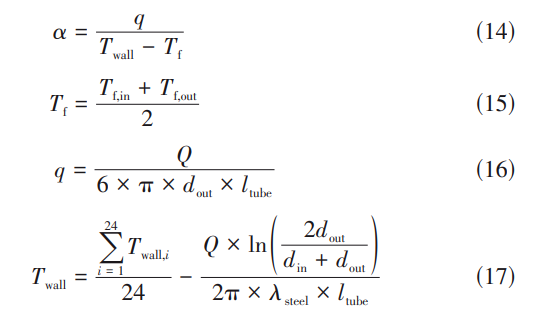
式中,α為傳熱系數(shù),W/(m2.K);q為熱流密度,W/m2;Twall為繞管外壁面溫度,K;Tf為流體溫度,K;Tf,in為流體入口溫度,K;Tf,out為流體出口溫度,K;Q為加熱功率,W;din為繞管內(nèi)徑,m;dout為繞管外徑,m;ltube為繞管長度,m;Twall,i為傳熱測試段內(nèi)壁面溫度,K;λsteel為不銹鋼熱導(dǎo)率,取13.81W/(m.K)。實驗系統(tǒng)所用質(zhì)量流量計、壓差變送器、壓力變送器、熱電偶等具體參數(shù)見表1。
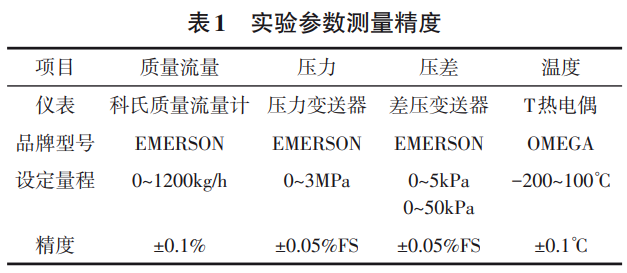
3、模型驗證和結(jié)果分析
3.1干度及質(zhì)流密度對壓降的影響
在入口壓力為0.3MPa的條件下研究不同干度及質(zhì)流密度對殼側(cè)壓降的影響。通過數(shù)值計算,得到壓降與干度和質(zhì)流密度的關(guān)系,如圖5所示。其中多數(shù)模擬偏差在±20%以內(nèi)。
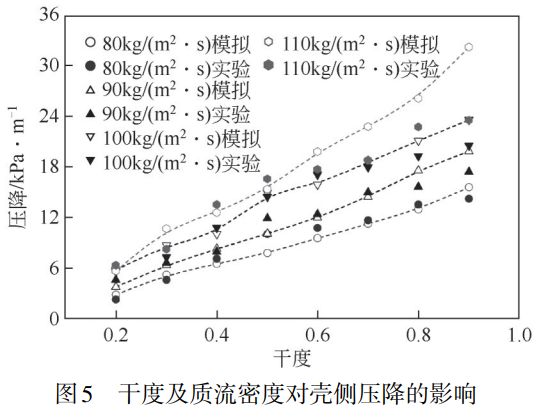
從壓降圖中可以看出,隨著干度和質(zhì)流密度的增加,殼側(cè)壓降呈現(xiàn)出不斷增大的趨勢。殼側(cè)壓降主要受液相與管壁間的黏性力和氣相剪切力的作用。當(dāng)干度較小時,液相的流速較慢,流體與管壁間的黏性作用占主導(dǎo)地位,因此壓降較小。當(dāng)干度較高時,摩擦壓降主要取決于氣相流速,因此當(dāng)干度增加時氣相流速得到提升,導(dǎo)致了壓降的增加。
3.2干度及質(zhì)流密度對傳熱系數(shù)的影響
為驗證實驗與模擬之間的誤差,在質(zhì)流密度70kg/(m2.s)、熱流密度3000W/m2的條件下,傳熱系數(shù)隨干度(x)的變化如圖6(a)所示。從圖中可以看出實驗值與模擬值的變化規(guī)律吻合度較高,傳熱系數(shù)隨干度的增加而減小。該現(xiàn)象主要由于干度越小,工質(zhì)中液相質(zhì)量占比越少,難以覆蓋住完整的壁面。此外低干度時模擬值與實驗值間誤差較小,大部分誤差在±20%以內(nèi),在高干度時模擬值與實驗值誤差相比較大,主要存在兩方面原因:一方面,在實驗中,高干度下殼側(cè)氣相流速較高,測量儀器數(shù)值波動范圍較大;另一方面,干度大于0.7時,氣液相滑速比相差較大,預(yù)期會部分增加模擬與實驗的誤差。圖6(b)顯示了0.3MPa蒸發(fā)壓力、60~120kg/(m2.s)質(zhì)流密度、1000~4000W/m2熱流密度條件下,模型的預(yù)測值與實驗值的比較。由圖6(b)可以看出模擬結(jié)果與實驗值的偏差大部分在±40%以內(nèi)。
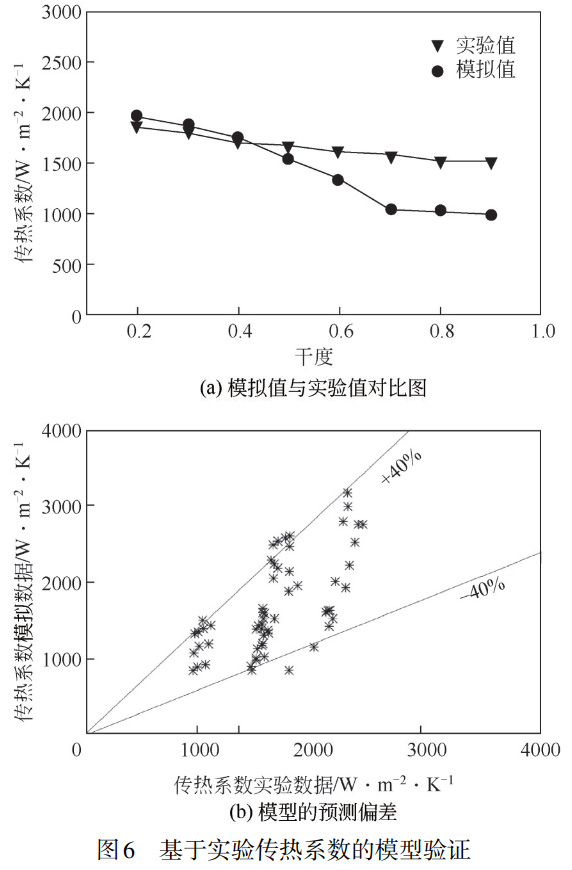
在入口壓力為0.3MPa、熱流密度為3000W/m2的條件下,不同干度及質(zhì)流密度下殼側(cè)傳熱系數(shù)的變化經(jīng)數(shù)值計算如圖7所示。從圖中可以看出傳熱系數(shù)隨干度的增加而減小,當(dāng)干度降到0.7時,傳熱系數(shù)趨于穩(wěn)定。產(chǎn)生該規(guī)律的原因可能是絕大部分工況下液相較多,換熱器殼程內(nèi)的換熱主要得益于繞管壁面液相的傳導(dǎo)作用,隨著干度的增大,液相工質(zhì)減少并且氣相對其剪切力增大,導(dǎo)致液膜越來越難以覆蓋住管壁面,管壁出現(xiàn)局部蒸干區(qū),且隨干度的增大,蒸干區(qū)變大,傳熱系數(shù)減小,加強了傳熱惡化。當(dāng)干度為0.7時,氣相的對流換熱占據(jù)主導(dǎo)地位,此后干度的繼續(xù)增加對傳熱系數(shù)已無明顯影響,傳熱趨于穩(wěn)定。此外,圖中結(jié)果表明,相同干度下,傳熱系數(shù)隨質(zhì)流密度的增加而增加。這是因為液相流量的增加使得液膜能夠覆蓋住更大的管壁面積,繞管式換熱器殼側(cè)整體換熱效果得到加強。
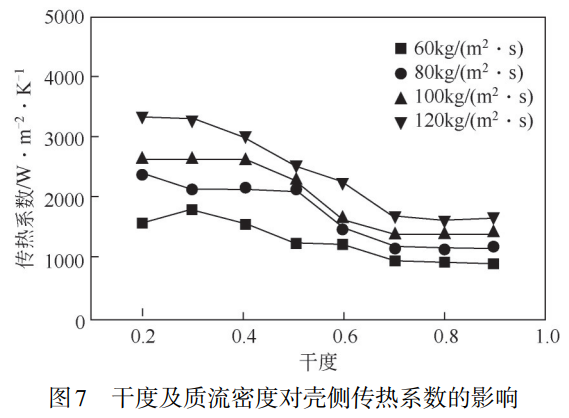
3.3流型轉(zhuǎn)變結(jié)果
殼側(cè)壓降及傳熱特性變化規(guī)律均與管壁面流型有著密不可分的聯(lián)系,因此流型隨干度的變化規(guī)律尤為重要。在繞管氣液相傳質(zhì)過程中,靠近壁面處氣泡首先成核,不斷增大后穿過液膜,在氣液相密度差引起的浮力作用下,部分氣泡被迫聚集在繞管壁面下方,并沿管徑方向移動。此外,由于氣泡的不斷膨脹使得壁面液膜產(chǎn)生了波動,不同管徑處的流量產(chǎn)生了變化,使得不同區(qū)域產(chǎn)生不均勻傳熱的同時也加快了流型的轉(zhuǎn)變。在實驗工況的范圍內(nèi),主要出現(xiàn)的流型主要包括柱狀流、滴狀流、剪切流和霧狀流,如圖8所示。在60kg/(m2.s)質(zhì)流密度下,實驗結(jié)果表明干度為0.2時,殼側(cè)氣體流量較小,流速較慢,此時液膜呈連續(xù)不間斷的柱狀;隨著干度增加至0.5時,減少后的液相流量已無法呈現(xiàn)出連續(xù)不間斷的流型,轉(zhuǎn)而變?yōu)殡x散的滴狀流;當(dāng)干度上升至0.7時,液相流量急劇減少,且氣相流速較大,此刻管壁面幾乎沒有液膜覆蓋,壁面出現(xiàn)蒸干區(qū),殼側(cè)流型呈剪切流;當(dāng)干度上升至0.9時,殼側(cè)幾乎全為氣相,管壁面蒸干區(qū)占據(jù)主體,流型變?yōu)殪F狀流。在當(dāng)前實驗條件下,流型轉(zhuǎn)化過程較為清晰且與模型研究結(jié)果相一致。模擬結(jié)果中流型變化隨干度變化的趨勢保持一致:柱狀流主要在干度為0.2時呈現(xiàn),而滴狀流則主要在干度為0.5附近出現(xiàn),剪切流在干度為0.7附近出現(xiàn),霧狀流在干度為0.9附近出現(xiàn)。不同干度下的流型變化同時也有對應(yīng)條件下的殼側(cè)換熱情況的轉(zhuǎn)變。結(jié)合圖7與圖8,可以看出,在干度為0.2、0.5、0.7和0.9附近區(qū)域,都是傳熱系數(shù)的趨勢發(fā)生轉(zhuǎn)折變化的區(qū)域,二者緊密相關(guān)。
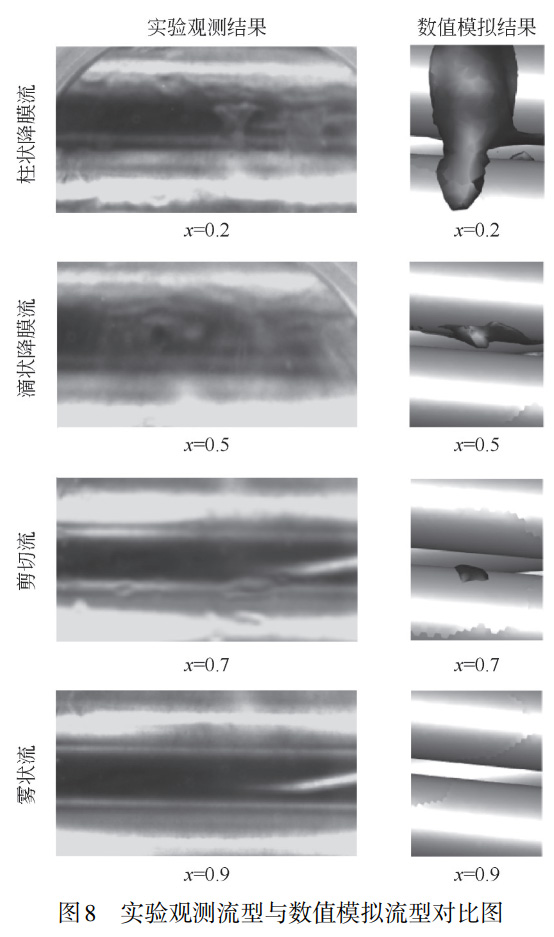
4、結(jié)論
本研究針對LNG繞管式換熱器殼程兩相流動構(gòu)建了沸騰傳熱模型,并通過實驗驗證,探索了壓降、傳熱系數(shù)及流型變化規(guī)律,主要結(jié)論如下。
(1)通過數(shù)值模型計算得到的壓降值與實驗數(shù)據(jù)具有較高的吻合度。壓降誤差在±20%以內(nèi),傳熱誤差則多在±40%以內(nèi)。
(2)數(shù)值模型計算得到的換熱系數(shù)顯示,在相同工況下,傳熱系數(shù)隨干度的增加而減小,當(dāng)干度到0.7時趨于穩(wěn)定,且質(zhì)流密度的增大對加強換熱有顯著效果。
(3)根據(jù)實驗,混合烴類制冷劑在殼側(cè)流動中,按不同干度依次呈現(xiàn)出柱狀流、滴狀流、剪切流和霧狀流四種流型,轉(zhuǎn)換干度分別為0.2、0.5、0.7和0.9,且與模擬結(jié)果吻合。
參考文獻
[1] 李豐志, 于佳文, 鹿來運, 等. LNG繞管式換熱器管側(cè)流動與傳熱實 驗臺設(shè)計及驗證[J]. 哈爾濱工業(yè)大學(xué)學(xué)報, 2017, 49(2): 98-102.
LI Fengzhi, YU Jiawen, LU Laiyun, et al. Design and verification for tube-side flow and heat transfer test-rig of coil-wound LNG heat exchangers[J]. Journal of Harbin Institute of Technology, 2017, 49(2): 98-102.
[2] 歐陽新萍, 秦潔, 薛林鋒, 等. 多股流繞管式換熱器的管束排布及傳 熱計算[J]. 化工進展, 2019, 38(S1): 39-45.
OUYANG Xinping, QIN Jie, XUE Linfeng, et al. Tube bundle arrangements and heat transfer calculations of multi-stream spiral wound heat exchanger[J]. Chemical Industry and Engineering Progress, 2019, 38(S1): 39-45.
[3] LI J R, HU H T, WANG H X. Numerical investigation on flow pattern transformation and heat transfer characteristics of two-phase flow boiling in the shell side of LNG spiral wound heat exchanger[J]. International Journal of Thermal Sciences, 2020, 152: 106289.
[4] 邱國棟, 蔡偉華, 吳志勇, 等. 繞管換熱器兩相流冷凝換熱及沿程壓 力降模擬[J]. 煤氣與熱力, 2015, 35(2): 30-34.
QIU Guodong, CAI Weihua, WU Zhiyong, et al. Simulation of twophase flow condensing heat exchange and frictional pressure drop in coil-wound heat exchangers[J]. Gas & Heat, 2015, 35(2): 30-34.
[5] 吳志勇, 陳杰, 浦暉, 等. LNG繞管式換熱器殼側(cè)過熱態(tài)流動的數(shù)值 模擬[J]. 煤氣與熱力, 2014, 34(8): 6-11.
WU Zhiyong, CHEN Jie, PU Hui, et al. Numerical simulation of superheated flow of refrigerant at shell side of LNG spiral wound heat exchanger[J]. Gas & Heat, 2014, 34(8): 6-11.
[6] 王斯民, 段旭東, 文鍵. 直插式墊條型纏繞管式換熱器過程強化[J].化工進展, 2021, 40(12): 6613-6619.
WANG Simin, DUAN Xudong, WEN Jian. Comprehensive performance of spiral-winding tube heat exchanger with vertically inserting space bars[J]. Chemical Industry and Engineering Progress, 2021, 40(12): 6613-6619.
[7] 楊發(fā)煒, 張周衛(wèi), 周文和. 纏繞管式換熱器并管殼程換熱數(shù)值研究[J]. 石化技術(shù), 2022, 29(5): 96-100.
YANG Fawei, ZHANG Zhouwei, ZHOU Wenhe. Numerical study on shell side heat transfer of wound tube heat exchanger[J]. Petrochemical Industry Technology, 2022, 29(5): 96-100.
[8] HE N, CHEN Y D, YU S R, et al. Effect of winding angles on flow and heat transfer characteristics in the shell side of spiral wound heat exchangers[J]. Thermal Science and Engineering Progress, 2022, 29: 101226.
[9] 馬飛. 螺旋纏繞管換熱器傳熱數(shù)值模擬[D]. 鄭州: 鄭州大學(xué), 2014. MA Fei. Numerical simulation of heat transfer of spiral coiledheat exchanger[D]. Zhengzhou: Zhengzhou University, 2014.
[10] 汪耀龍, 劉蓮, 鄭文科, 等. 均布器對LNG繞管式換熱器殼側(cè)流體 的影響[J]. 煤氣與熱力, 2022, 42(5): 16-22.
WANG Yaolong, LIU Lian, ZHENG Wenke, et al. Influence of distributor on shell-side fluid of LNG spiral wound heat exchanger[J]. Gas & Heat, 2022, 42(5): 16-22.
[11] NEERAAS B O, FREDHEIM A O, AUNAN B. Experimental shellside heat transfer and pressure drop in gas flow for spiral-wound LNG heat exchanger[J]. International Journal of Heat and Mass Transfer, 2004, 47 (2): 353-361.
[12] NEERAAS B O, FREDHEIM A O, AUNAN B. Experimental data and model for heat transfer, in liquid falling film flow on shell side for spiral wound LNG heat exchanger[J]. International Journal of Heat and Mass Transfer, 2004, 47 (14/15/16): 3565-3572.
[13] SUN C, LI Y, HAN H, et al. Effect of compound sloshing conditions on pressure drop and heat transfer characteristics for FLNG spiral wound heat exchanger[J]. Applied Thermal Engineering, 2019, 159: 113791.
[14] HU H, DING C, DING G, et al. Heat transfer characteristics of twophase mixed hydrocarbon refrigerants flow boiling in shell side of LNG spiral wound heat exchanger[J]. International Journal of Heat and Mass Transfer, 2019, 131: 611-622.
[15] 龐曉冬, 楊果成, 陳杰, 等. 丙烷在螺旋折流板管殼式換熱器殼側(cè)流 動冷凝換熱特性的實驗研究[J]. 制冷技術(shù), 2016, 36(5): 31-37.
PANG Xiaodong, YANG Guocheng, CHEN Jie, et al. Experimental investigation of heat transfer characteristics of propane condensation in helical baffle shell-tube heat exchanger[J]. Chinese Journal of Refrigeration Technology, 2016, 36(5): 31-37.
[16] ZHU J, SUN C, LI Y, et al. Experiment on adaptability of feed gas flow rate and sea conditions on FLNG spiral wound heat exchanger[J]. International Journal of Heat and Mass Transfer, 2019, 138: 659-666.
[17] SUN C, LIU L, WANG S, et al. Visualization experimental and numerical study on multiphase flow characteristics of main cryogenic heat exchanger in offshore liquefied natural gas industry chain[J]. Cryogenics, 2022, 124: 103490.
[18] ZHENG W, CAI W, JIANG Y. Distribution performance of gas–liquid mixture in the shell side of spiral-wound heat exchangers[J]. Chinese Journal of Chemical Engineering, 2019, 27 (10): 2284-2292.
[19] 邱中建, 趙文智, 胡素云, 等. 我國天然氣資源潛力及其在未來低碳 經(jīng)濟發(fā)展中的重要地位[J]. 中國工程科學(xué), 2011, 13(6): 81-87.
QIU Zhongjian, ZHAO Wenzhi, HU Suyun, et al. The natural gas resource potential and its important status in the coming low-carbon economy[J]. Engineering Sciences, 2011, 13(6): 81-87.
[20] 丁超 . LNG 繞管式換熱器殼側(cè)兩相流動與傳熱特性實驗研究[D].上海: 上海交通大學(xué), 2018.
DING Chao. Experimental investigations on two-phase flow and heat transfer characteristics in shell side of LNG spiral-wound heat exchanger[D]. Shanghai: Shanghai Jiao Tong University, 2018.
[21] 董龍飛, 劉坤. LNG 繞管式換熱器殼程兩相降膜換熱的數(shù)值模擬[J]. 石油化工高等學(xué)校學(xué)報, 2020, 33(5): 80-85. DONG Longfei, LIU Kun. Numerical simulation of two-phase falling film heat transfer at shell side of spiral-wound LNG heat exchanger[J]. Journal of Petrochemical Universities, 2020, 33(5): 80-85.
[22] WEICKERT T, GRAB T H, STORCH T H, et al. Investigations regarding the wetting behavior of propane on the surfaces of geothermal heat pipes[C]//The 8th Minsk International Seminar Heat Pipes, Heat Pumps, Refrigerators, power Sources. Minsk, 2011.
[23] 陳永東, 吳曉紅, 周兵. LNG纏繞管式換熱器試驗研究中的熱物性 計算方法[J]. 天然氣工業(yè), 2011, 31(6): 92-97.
CHEN Yongdong, WU Xiaohong, ZHOU Bing. Calculation methods of thermo-physical properties for experimental research on LNG spiralwound heat exchangers[J]. Natural Gas Industry, 2011, 31(6): 92-97.
[24] FREDHEIM A O. Thermal design of coil-wound LNG heat exchanger. Shell-side heat transfer and pressure drop[D]. Norway: Trondheim University, 1994.
[25] KUNZ O, WAGNER W. The GERG2004 Wide-range equation of state of natural gases and other mixtures[J]. Journal of Chemical and Engineering Data, 2007, 57(11): 3032-3091.
相關(guān)鏈接